The highway section between Mandal and Kristiansand is part of a gigantic new road-building project that aims to improve access to Norway’s west coast. Located next to Mandal fjord in Brennevinsmyra and equipped with its very own jetty is the new Benninghoven RPP 4000 plant. In operation since August 2021, this is Norway’s most innovative, advanced, and environmentally friendly asphalt facility. Fitted with a recycling drum working on the countercurrent principle and featuring a hot-gas generator, the plant achieves recycling input rates of up to 100 percent while keeping emissions within compliant ranges. This ticks all the boxes for operating company Velde Produksjon,: the features offered by this plant set the standard for the future of asphalt production in Norway and are especially economical.
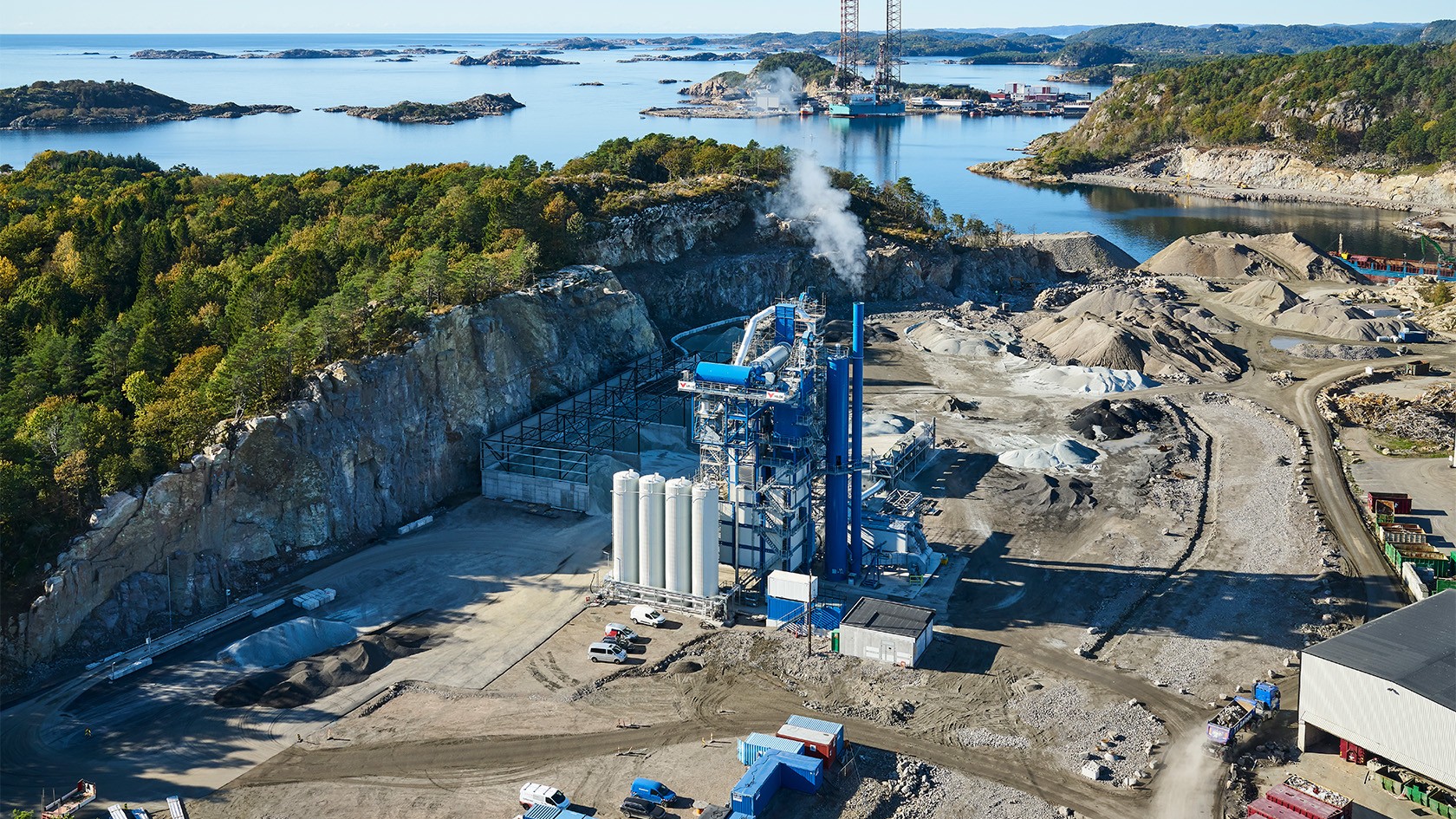