Nello stabilimento principale di Tirschenreuth possono essere prodotti ogni anno fino a 20.000 rulli. Poiché i rulli tandem sono dotati di due tamburi, Hamm necessita di un numero ben più elevato di 20.000 tamburi all'anno. I tamburi vengono realizzati just-in-time nello stabilimento di tamburi di oltre 11.000 m². In questo modo, grazie anche a tempi di riassortimento brevi, Hamm è in grado di reagire in modo molto flessibile e veloce alle richieste del mercato.
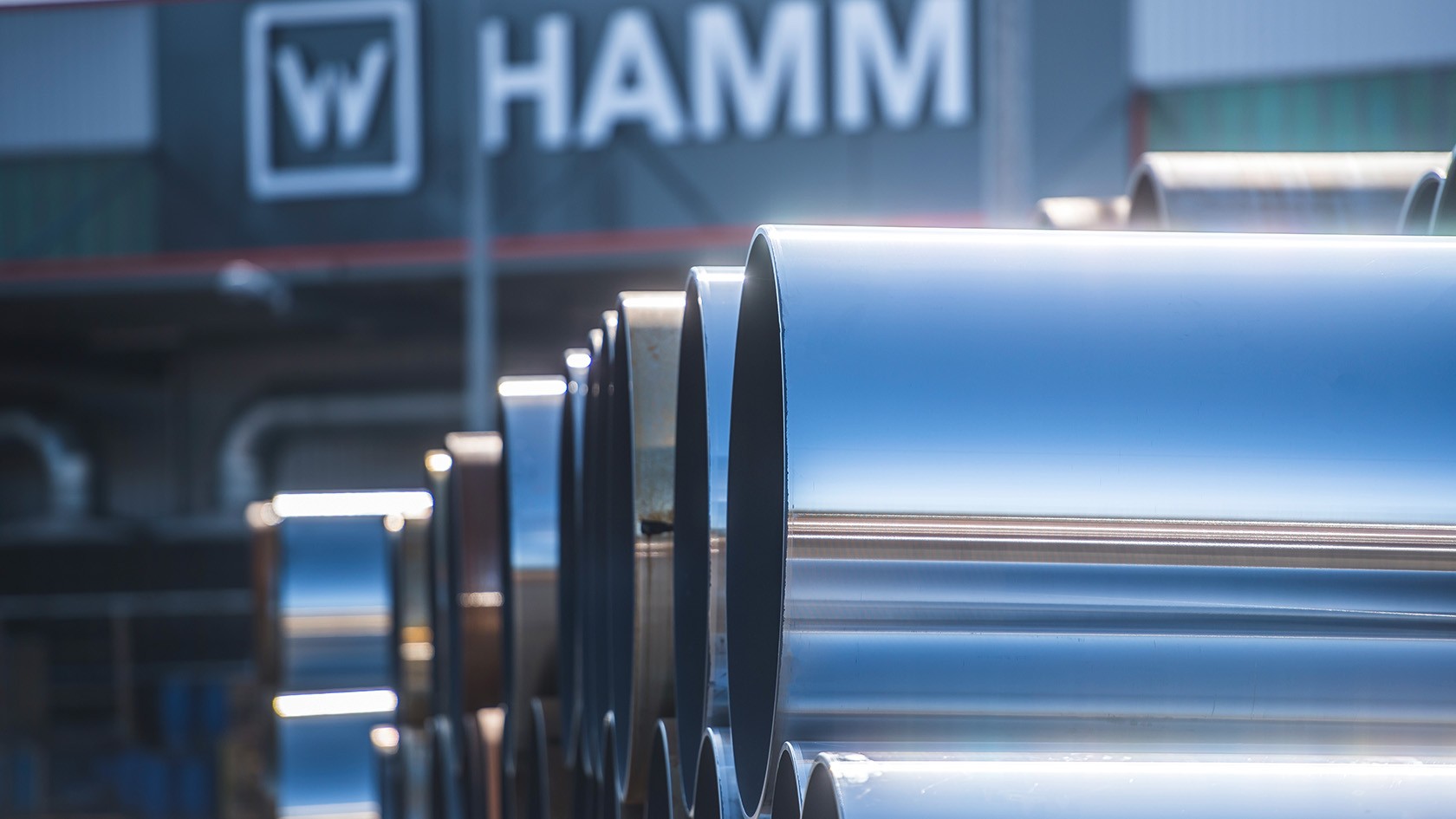