The main plant in Tirschenreuth can produce up to 20,000 rollers per year. Since tandem rollers are equipped with two drums, Hamm requires considerably more than 20,000 drums per year. They are produced just-in-time in a drum plant with an area of over 11,000 m². Thanks to this and short scheduling times, Hamm can respond very flexibly and quickly to market demands.
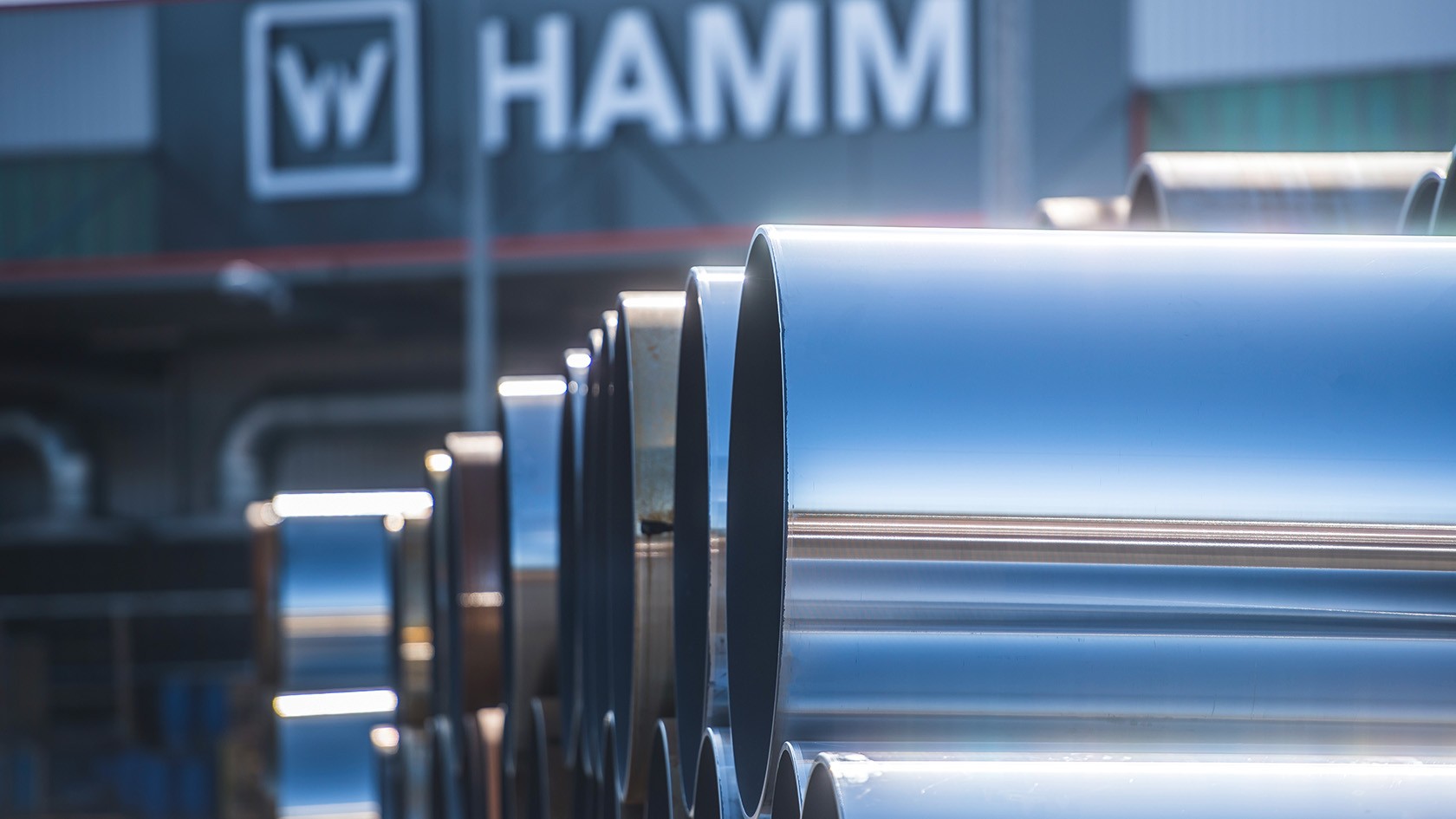