L'usine mère de Tirschenreuth peut produire jusqu'à 20 000 compacteurs par an. Les rouleaux tandem étant équipés de deux rouleaux, Hamm a besoin de bien plus de 20 000 rouleaux par an. Ils sont produits juste-à-temps dans l'usine de rouleaux couvrant plus de 11 000 m². Grâce à cela et aux délais de mise à disposition courts, Hamm peut réagir très rapidement et en toute flexibilité aux exigences du marché.
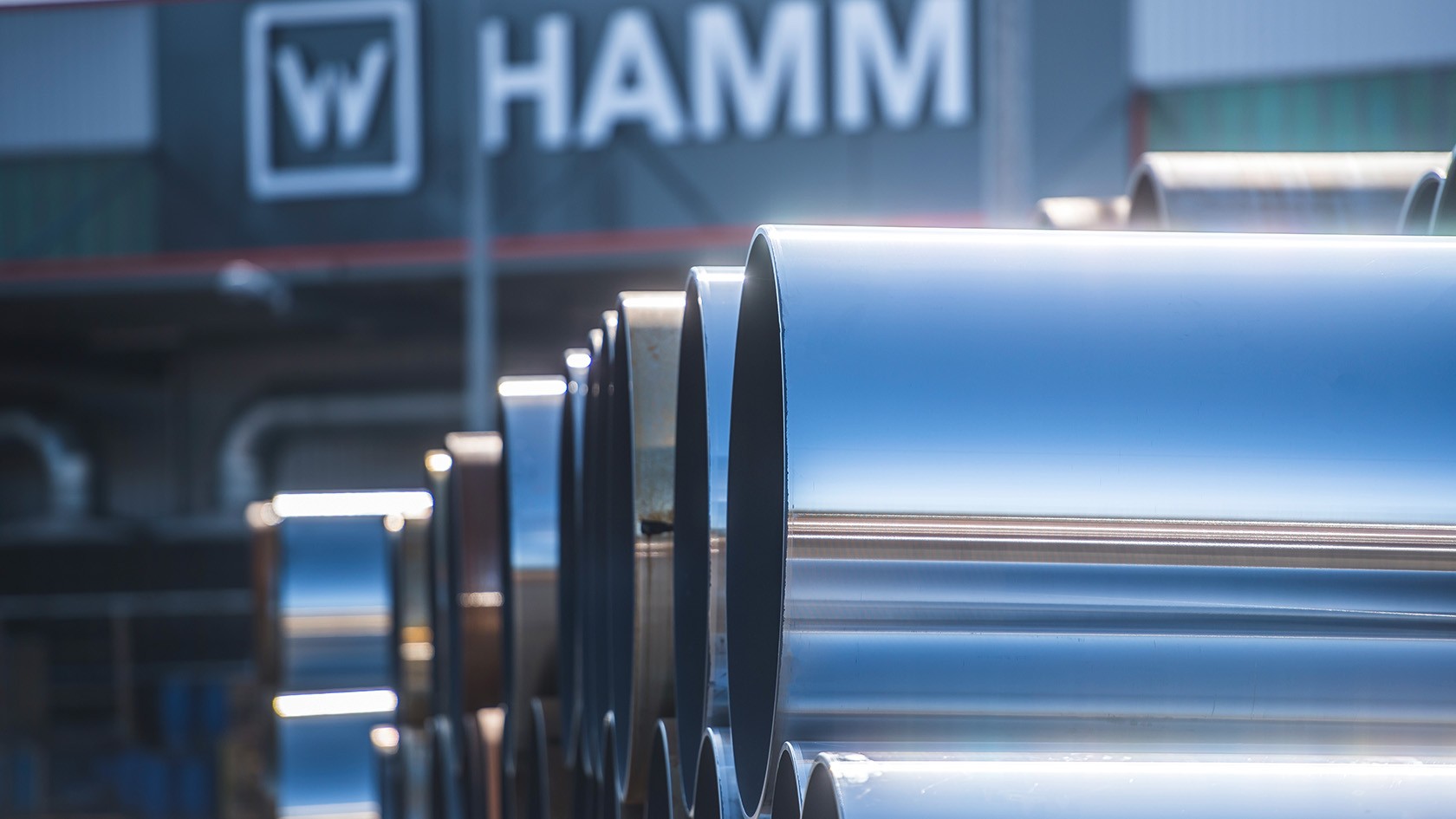