En la planta central de Tirschenreuth se pueden fabricar hasta 20 000 rodillos al año. Como los rodillos tándem están equipados con dos tambores, Hamm necesita algo más de 20 000 tambores al año. En la planta de tambores de más de 11 000 m² se fabrican justo a tiempo. Gracias a esto y a los cortos plazos de disposición, Hamm puede reaccionar con gran rapidez y flexibilidad a las exigencias del mercado.
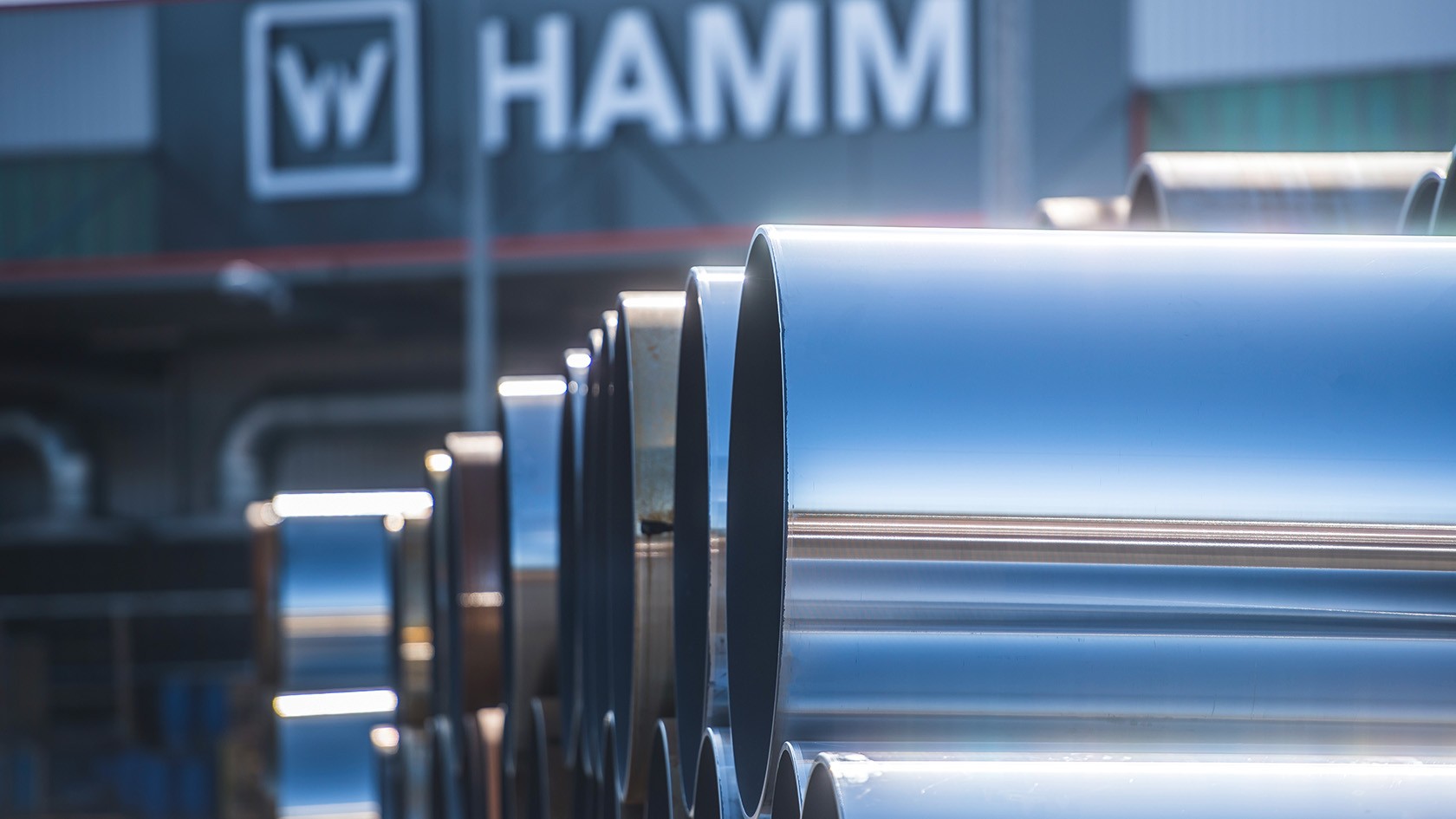