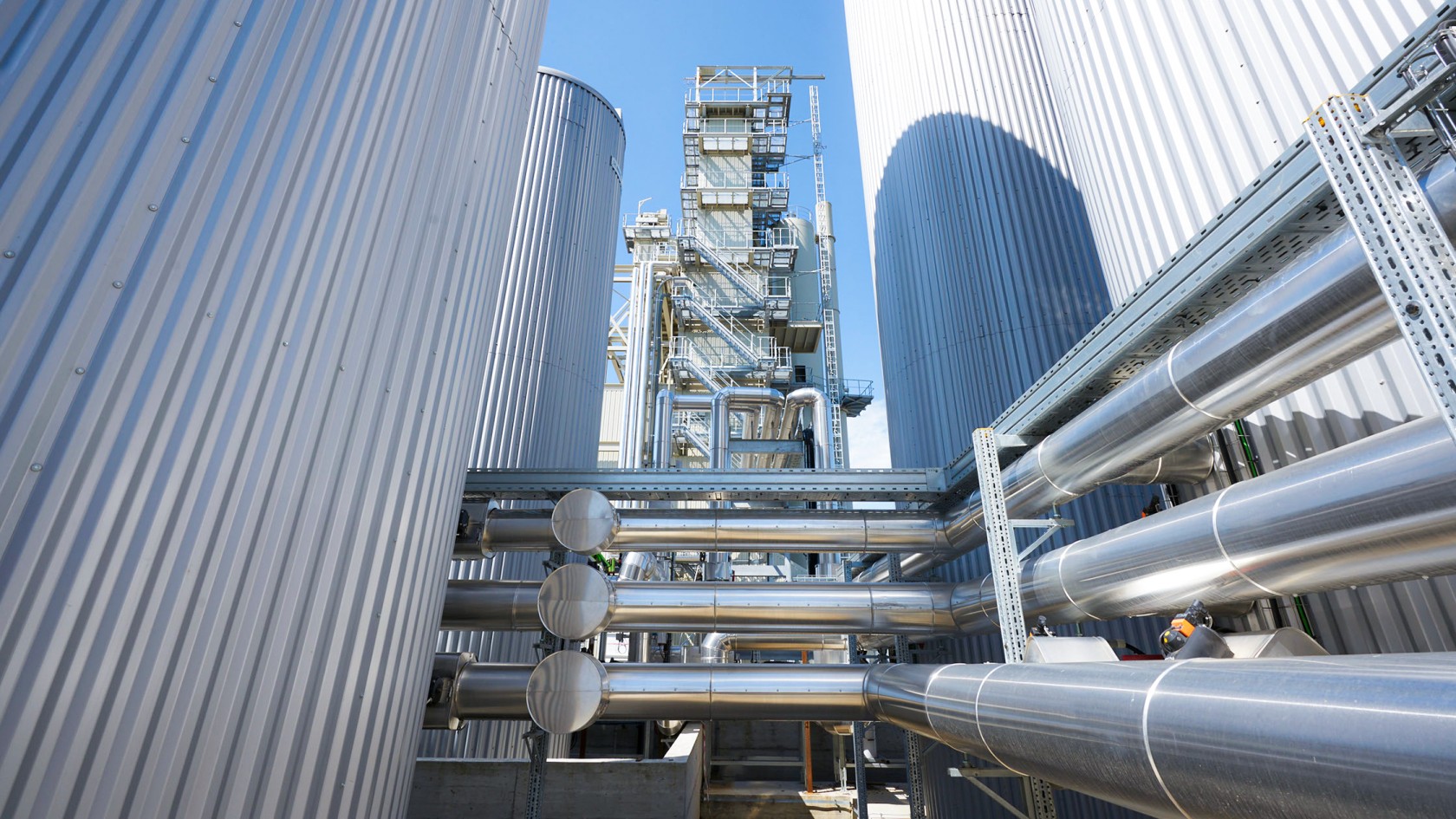
Großmehring | Bavaria, Germany
IAM Ingolstädter Asphaltmischwerke GmbH & Co. KG has been operating an asphalt mixing plant at the Großmehring site near Ingolstadt in southern Germany for many decades. During this period, the company already commissioned several retrofit projects from Benninghoven. Most recently, the bitumen tanks had to be replaced. With this investment, IAM were able to increase the storage capacity as well as the flexibility of the plant and will be able to meet a variety of different customer demands. In addition to this, the new modules lower operating costs and benefit the environment.
The asphalt mixing plant in Großmehring has been supplying high-quality asphaltic mixtures since 1981. The mixtures are used to surface motorways as well as secondary and inner-city roads. IAM is part of the Geiger Group, a leading member of the German Asphalt Association. “High-quality asphalt and compliance with the applicable quality standards are accordingly important to us,” says Rainer Hohenwarter, Managing Director of the Geiger Group and Board Member of the German Asphalt Association (DAV).
To keep the plant state-of-the-art, the Geiger Group implemented several retrofit projects in collaboration with Benninghoven. This involved replacing the burner, installing a new dryer drum and integrating a user-friendly Benninghoven control.
“Retrofits from Benninghoven allow us to always deliver high quality, even when recipes change.”
Rainer Hohenwarter, Managing Director
Geiger Group
Ingolstädter Asphaltmischwerke have now used the replacement of the bitumen tanks, including all pipes, to convert the heating system from thermal oil to electricity and to expand the variety of stored bitumen. The calculations by the retrofit experts from the Benninghoven technical office had shown that this type of heating, which works without any local emissions, is a significant advantage for the selected tank configuration.
“We now have tanks with more storage capacity, some of which are equipped with a mixing nozzle or an agitator. That increases our flexibility, because we can now also store polymer modified bitumen (PmB). This means that we can produce a significantly larger number of recipes at the press of a button,” Managing Director Herbert Geiger, son of the company founder and longstanding head of the Group, reports enthusiastically.
Two of the new tanks have a capacity of 60 m³, while three others can hold 100 m³. That is significantly more than before. The higher storage capacity also supports flexibility, in particular when it comes to production reliability, because it is now easier to buffer delayed bitumen deliveries. Due to the better insulation of the tanks that IAM ordered, all five tanks can now maintain their temperature even better while using less heating energy. The mineral wool insulation is 300 mm thick and is protected with an outer layer of profiled sheeting.
The requirements from the Geiger Group were not just limited to producing and delivering bitumen tanks. The ancillary work presents the greatest challenge during the integration of bitumen tanks such as here in Bavaria: All pipes have to be connected to the infrastructure of the plant and the cables have to be connected to the plant control. That is why Benninghoven offers customers everything from a single source for its retrofit projects: From consulting and planning to installation and commissioning, the Benninghoven team complete all their tasks in a highly reliable manner – until everything works and has been implemented to the full satisfaction of the customer and its employees.
“At our site in Großmehring, all measures linked to new foundations should be avoided wherever possible. That is why we have already optimised many elements through retrofit projects with Benninghoven. The technology allow us to always deliver high quality, even when recipes change,” explains Managing Director Rainer Hohenwarter.
Highlights of the Benninghoven bitumen tanks