Foamed bitumen
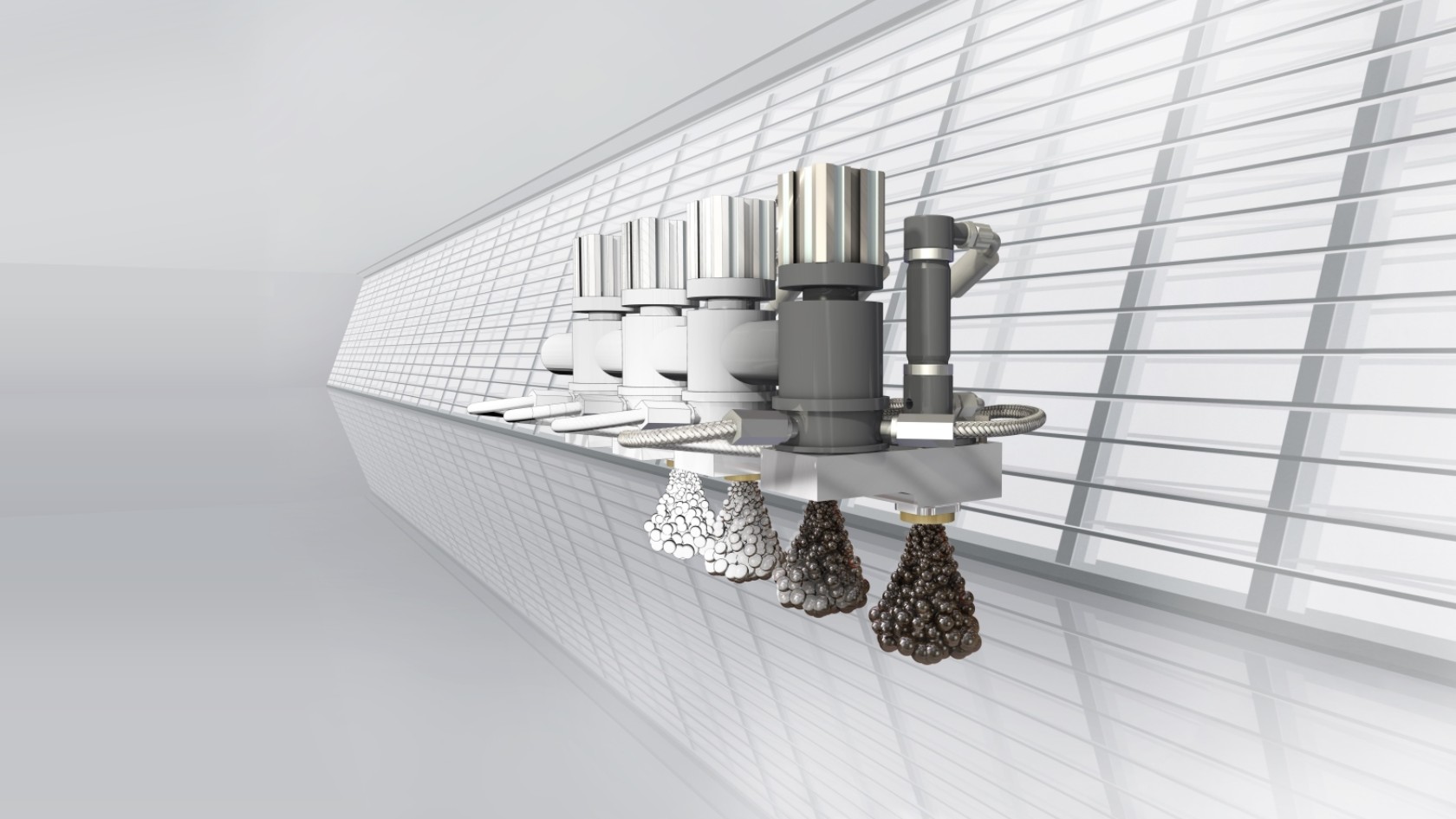
Cold recycling with foamed bitumen has become an established technology worldwide and is now increasingly moving into the focus of road authorities and construction companies for use in the rehabilitation and new construction of road pavements. Cold recycling with foamed bitumen produces flexible and highly durable base layers. Being a part of the pavement structure, these are the perfect foundation for the final asphalt overlay to be built at reduced layer thickness. Foamed bitumen is produced from approx. 175 °C hot road-grade bitumen using state-of-theart technology. Microprocessor-controlled injection systems installed in the WIRTGEN recyclers produce the foamed bitumen and inject it into the mineral aggregate in precisely metered quantities.
In excess of 100 million square metres have meanwhile been recycled in numerous countries around the world using foamed bitumen as binding agent.
Foamed bitumen is produced by foaming standard road-grade bitumen. In the process, small amounts of water and air are injected into the hot bitumen at high pressure, which results in the bitumen foaming and expanding to around 20 times its original volume. The bitumen foam is then injected into a mixer via injection nozzles. It is eminently suitable for mixing with cold and moist construction materials. The new material – frequently produced using reclaimed asphalt pavement (RAP) – is called BSM (bitumen - stabilized material).
Preliminary testing with the mobile WLB 10 S foamed bitumen laboratory unit enables the foamed bitumen quality to be precisely determined in the laboratory even prior to the start of construction. Extremely simple handling enables parameters such as the water quantity, air pressure and temperature to be varied quickly and easily. The quality of foamed bitumen is primarily described in terms of its expansion ratio and half-life. With the mobile WLB 10 S foamed bitumen laboratory unit and WLM 30 twin-shaft pugmill mixer, we have translated our many years of field experience into state-of-the-art laboratory technology. These machines allow suitable test specimens to be produced in next to no time at all.
The mix makes all the difference
The WLB 10 S foamed bitumen laboratory unit is used for:
For mix production in the road laboratory, the WLB 10 S is connected directly to the WLM 30 twin-shaft pugmill mixer. The foamed bitumen produced by the WLB 10 S is then injected into the mixing process taking place in the WLM 30. The materials are mixed precisely and without any losses. Mixes for the manufacture of test specimens are thus produced in next to no time.
Easy workability is one of the distinctive features of BSM mixes. When sufficiently moist, there are no time limitations for the subsequent compaction process. Yet another very important hallmark of BSM layers is that they can be opened to traffic temporarily immediately after completion. In many cases, the cold recycled layer is simply surfaced with a thin asphalt layer serving as a wearing course. Road maintenance interventions also focus on the asphalt surface course, leaving the cold recycled layer undisturbed. This approach pays off in low road maintenance costs.
Material structure
Cold mixes produced with foamed bitumen behave like a construction material with constant inter-particle friction but signifi cantly increased cohesion (adhesion force) and strength. This type of material is also called BSM (bitumen-stabilized material). BSM mixes do not involve coating of the aggregate but homogeneous mixing of the bitumen binder and aggregate. Typical bitumen quantities range between 1.5 % by mass and 2.5 % by mass of the mixed material. After final compaction, the material is characterized by good flexible properties and high bearing capacity. It has a proven track record around the globe.
Cold recycling in-situ
Cold recycling with foamed bitumen can be performed either in-situ (on site) or in-plant (in a mixing plant). When cold recycling in-situ, a cold recycler granulates the damaged road pavement while at the same time mixing in foamed bitumen, water and cement in the required quantities. This method produces a new, homogeneous construction material (BSM) in a single operation. The in-situ cold recyclers are equipped with a powerful milling and mixing rotor and an injection system. Some models are additionally fitted with a screed for paving and pre-compaction of the new material mix.
Construction materials in-situ
Generally, all granular construction materials – and RAP materials – are suitable for recycling with foamed bitumen. WIRTGEN recyclers granulate both the asphalt layer and the uderlying layer, mixing the material with foamed bitumen in-situ in a single operation. After compaction, a high-quality bituminous base layer has thus been produced that is capable of withstanding extremely high traffic loads.
Cold recycling in-plant
When cold recycling in-plant, the pavement material is removed and transported to a mobile cold mixing plant located in the vicinity of the construction site. The milled material is then processed with foamed bitumen, water and cement in the required quantities to produce a new, homogeneous cold mix (BSM) which is suitable for immediate placing true to line and level or can be placed in stockpile for later use.
State-of-the-art injection system
Highest quality guaranteed: a thermostat-controlled heating system maintains the specified operating temperature of the entire injection system at all times both prior to and during the foamed bitumen production. This feature dispenses with having to flush the system after breaks in operation or at the end of the working day. The foaming process and application rates are governed by microprocessor control.
RAP material in-plant
The RAP material recovered by a WIRTGEN cold milling machine can usually be processed right after milling or placed in stockpile for an extended period of time. The mobile WIRTGEN KMA 220 cold mixing plant uses this source material to produce cold mix in-plant for subsequent reuse by a VÖGELE asphalt paver.
Recovered and new materials
Materials recovered from existing pavements, recycling materials and new materials are processed using appropriate crushing and screening technology and are subsequently mixed with foamed bitumen in the KMA 220 cold mixing plant. All road construction materials with suitable grading characteristics are qualified for recycling with foamed bitumen.
Low overall costs
The pavement structures shown in the illustration are examples of three different construction classes. Due to low binder requirements, the use of reclaimed asphalt pavement and exceptionally quick completion times, these construction methods are especially economical in terms of construction costs. Additional significant reductions in cost can be achieved by reducing the thickness of the upper asphalt layers. Maintenance costs are also extremely low. Unlike conventional asphalt layers, BSM layers are not prone to cracking as a result of ageing. This requires only the thin asphalt surface course to be replaced as necessary, dispensing with the expensive replacement of the complete asphalt pavement. Bitumen-stabilized materials are increasingly used also in Public Private Partnership (PPP) projects due to their exceptional material properties and the advantages offered by this type of construction.
Full reuse
As foamed bitumen offers numerous advantages, it enjoys a prominent position among the range of binders used in road construction. Adding foamed bitumen to granulated asphalt enables the material to be recycled 100% even in cold condition. Significant reductions in CO2 emissions are possible as the source materials can be processed without prior heating. Low application rates of only 1.5% to 2.5% of the total mass result in low binder costs. Road-grade bitumen can be obtained worldwide and is suitable for immediate use without requiring additional processing. Construction materials mixed with foamed bitumen can be placed, compacted and reopened to traffic immediately, thus minimizing construction times and disruptions to traffic.