Surface Layer Rehabilitation
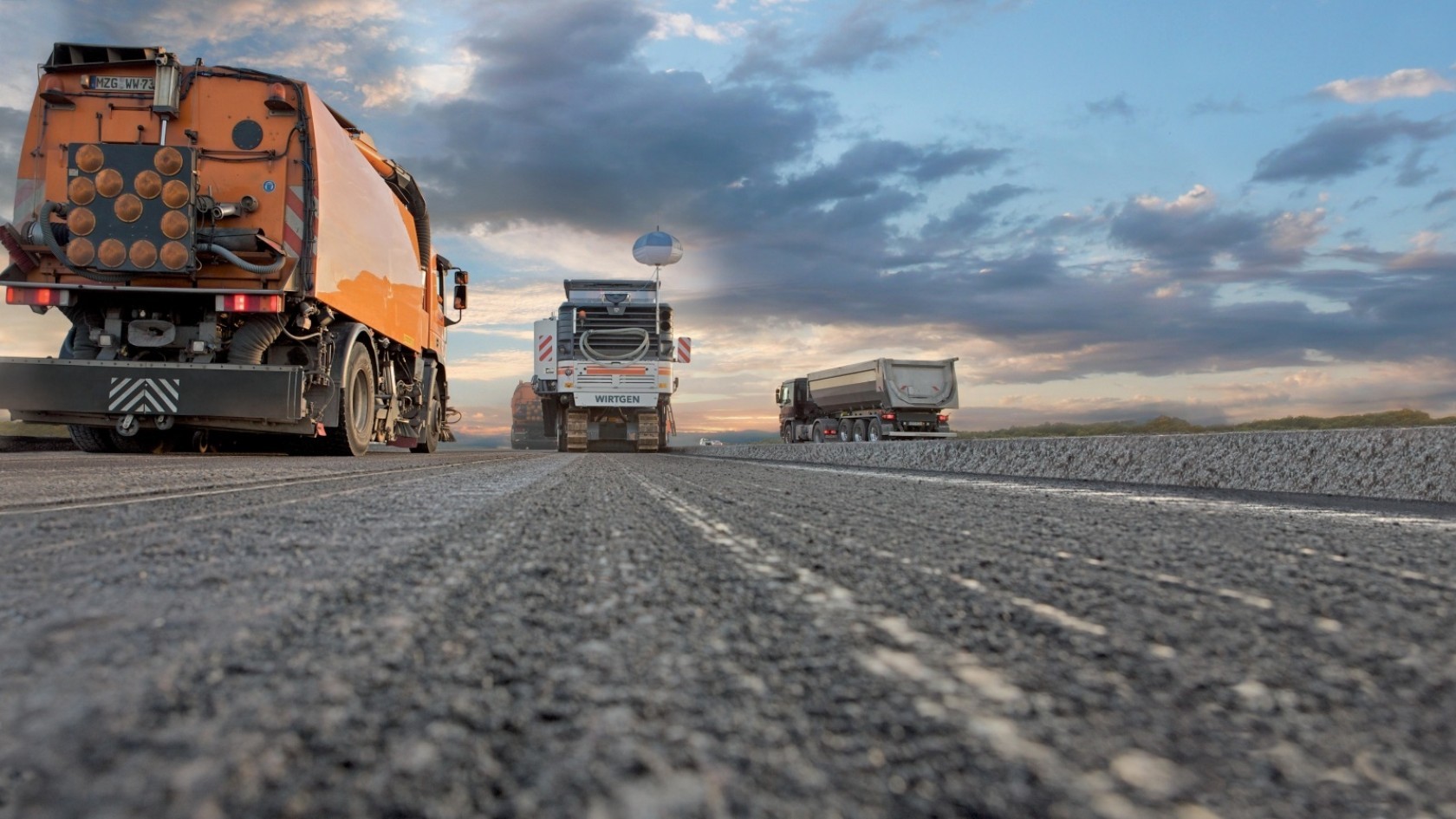
Replacing the pavement is a standard procedure when repairing roads. The challenge is to ensure that only the damaged layers of the road structure are removed - and to avoid disruptions to traffic at the same time. Under these conditions, cold milling is the only viable option for many construction projects
The tools that cold milling machines use for removing road layers were originally developed for the mining industry. So-called point-attack cutting tools, fitted to a rotating milling drum on the underside of the machine, bite into the road at precisely the specified depth. No material is too hard for these tools: Cold planers are even capable of rehabilitating concrete pavements. Whether asphalt or concrete: The material is milled and then directly loaded on trucks to be transported from site, all in one single pass.
Because traffic is often slow-moving in the area of the job site, car drivers mock the massive cold milling machines by saying that they’re always first in the traffic jam. Few bear in mind, however, that rehabilitation projects using cold milling machines are mostly carried out as mobile roadworks. Alternative methods would involve a much greater effort. Cold milling of road pavements is unrivalled in terms of both logistics and speed of execution.
Not all cold milling machines are as big as a whole apartment. Some models are as small as a passenger car. On many job sites, machines of different sizes frequently work as a team, each one playing its own aces: The large milling machine removes the large surfaces, while the small one takes care of milling off the pavement around “nuisances”, such as manhole covers or kerbstones.
Typical of rehabilitation projects using cold milling machines is that the removed layers are usually replaced with asphalt – irrespective of whether the damaged pavement was originally made of asphalt or concrete. This work is performed by road pavers. A road paver is capable of paving the new layers quickly and with outstanding quality. State-of-the-art automatic levelling systems make it possible to precisely adapt the height of the new surface layer to the existing pavement.
Rollers following directly behind the paver then carry out the final compaction of the new asphalt layer. When road pavers and rollers are busy at work on a job site, drivers also have reason to rejoice – this usually means that it won’t be long before traffic can flow freely once again.
Hamm following behind Vögele has proven to be a successful approach to surface layer reha-bilitation and road construction in general.
In this interview, Bernd Holl, Product Manager Cold Milling Machines at WIRTGEN, explains why cold milling is so important when replacing the pavement.
To the InterviewWheeled paver Universal Class
Basic width | 2.55 m |
Pave width, max. | 8 m |
Maximum laydown rate | 700 t/h |