Na fábrica principal em Tirschenreuth podem ser produzidos até 20.000 cilindros por ano. Devido ao fato dos rolos compactadores tandem serem equipados com dois cilindros, a Hamm necessita significativamente mais do que 20.000 cilindros por ano. Eles são fabricados "just-in-time" na fábrica de cilindros com mais de 11.000 m². Como resultado, e graças aos curtos tempos de disposição, a Hamm consegue reagir de forma muito flexível e rápida às exigências do mercado.
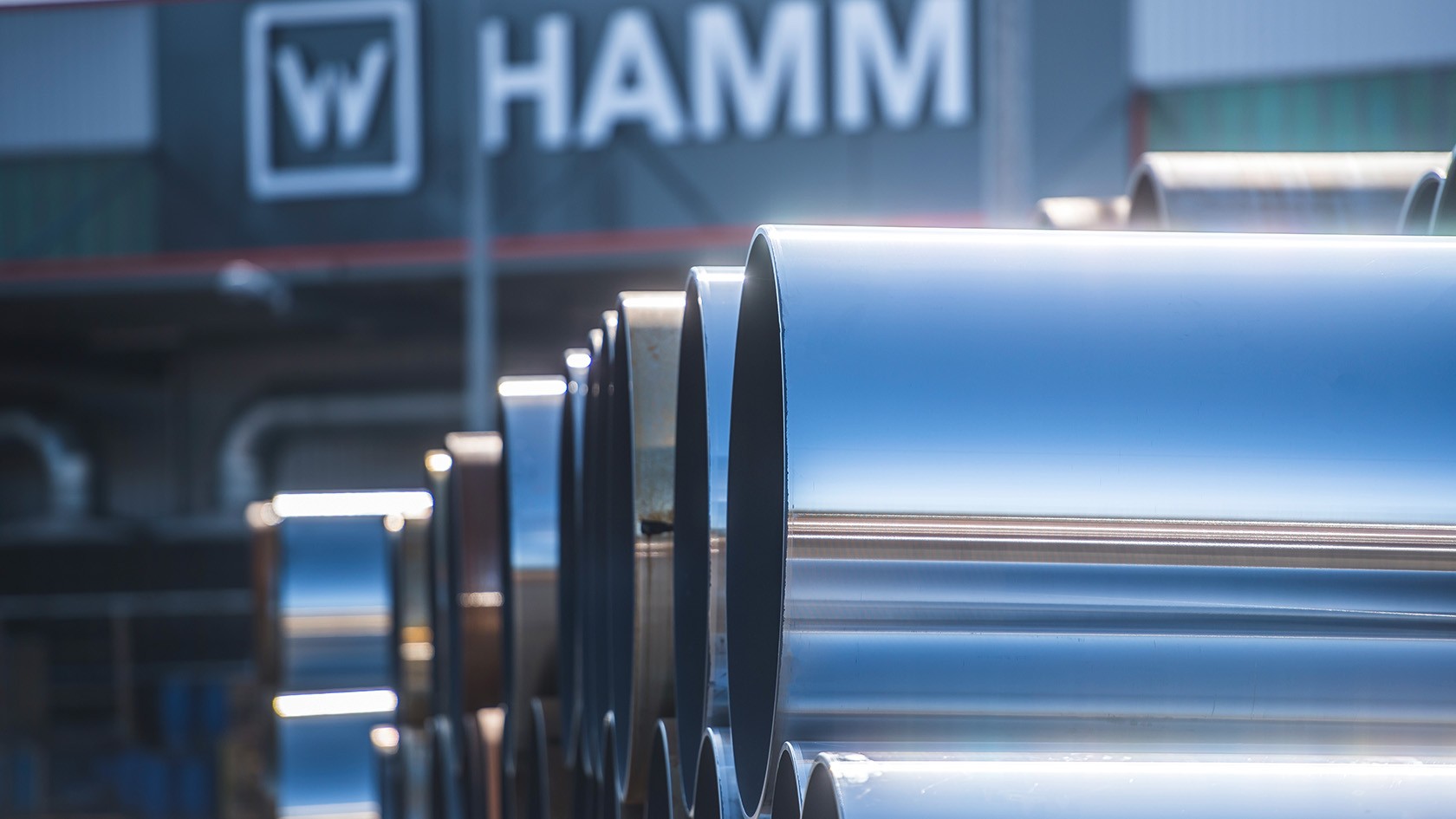