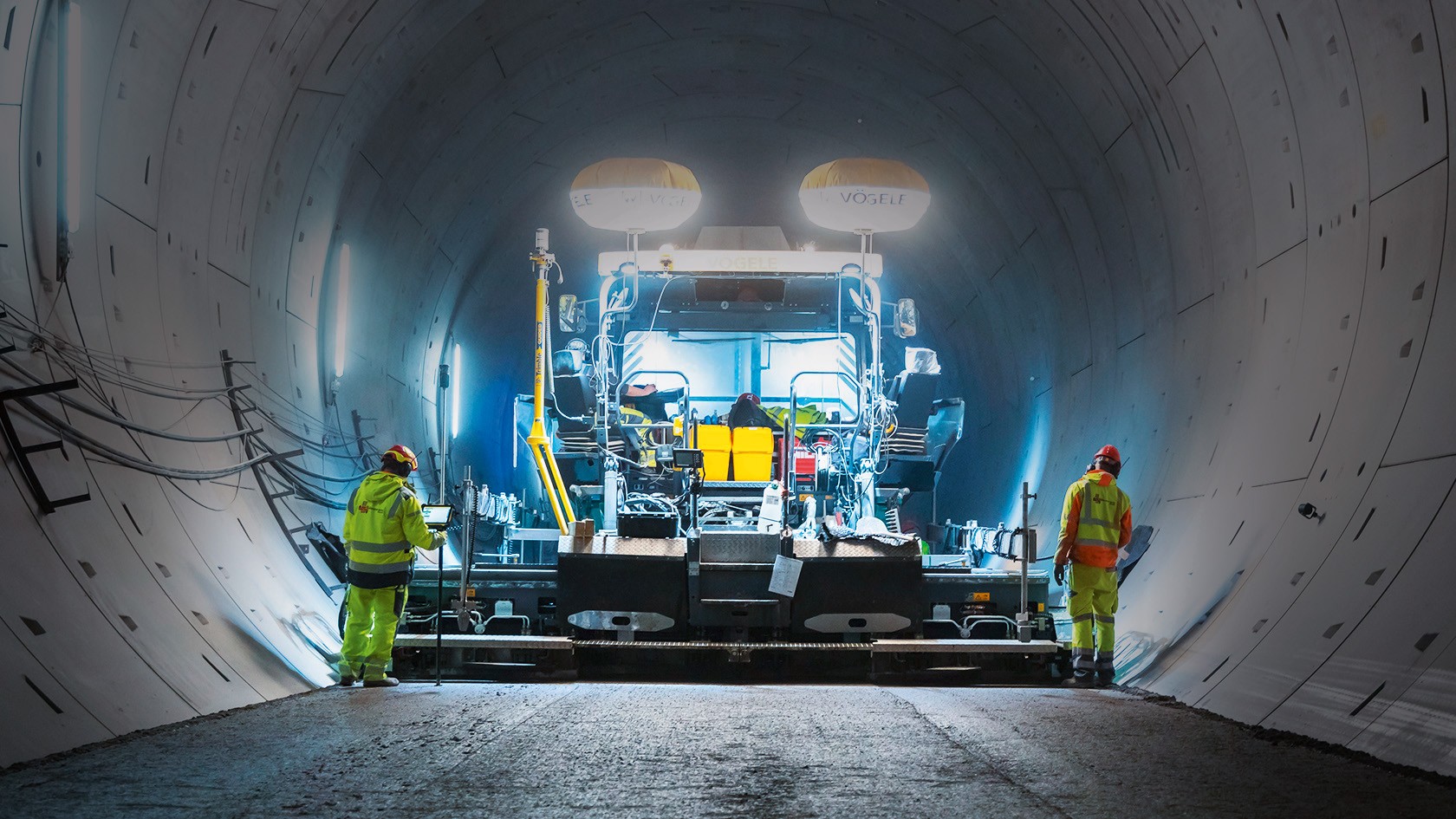
Grande progetto in una delle gallerie ferroviarie più lunghe della Germania: sul tratto di linea Stoccarda-Ulm, la finitrice SUPER 2100-3i, affiancata dall’alimentatore MT 3000-2i Offset, ha realizzato un binario senza ballast. Questa complessa sovrastruttura a sei strati doveva soddisfare requisiti elevatissimi.
Cinque strati di base uniti idraulicamente, requisiti elevatissimi di planarità e grandi sfide per la logistica: la posa in opera di un binario senza ballast in due canne lunghe 8 km del progetto Stoccarda-Ulm della Deutschen Bahn è stata davvero dura. La squadra di stesa ha affrontato questa sfida con la SUPER 2100-3i affiancata dal banco ad alta compattazione AB 600 TP2 e dal sistema di guida 3D. Un alimentatore MT 3000-2i Offset ha permesso di rendere più agevole la logistica di cantiere.
I progetti di costruzione stradale nelle gallerie ferroviarie sono estremamente complessi. Da un lato, la mancanza di spazio sul cantiere richiede il perfetto coordinamento di tutta la logistica. Dall’altro, le prescrizioni riguardanti il piano di piattaforma sono enormi: le linee ad alta velocità, infatti, devono essere assolutamente piane e resistere a sollecitazioni estreme, perché i convogli della Deutsche Bahn non solo viaggiano a velocità sempre più alte, ma diventano anche sempre più lunghi e con cadenze di servizio sempre più ravvicinate.
Per questo, nel Tunnel Albvorland di 8.176 m di lunghezza, una tratta del progetto Stoccarda-Ulm della Deutsche Bahn prevista per una velocità di 250 km/h, si doveva costruire un binario senza ballast. I binari senza ballast sono formati, solitamente, da uno strato antigelo, uno strato di base unito idraulicamente e uno strato in misto cementato o bitumato e, rispetto ai letti di pietrisco, sono nettamente più resistenti, duraturi e non richiedono pressoché alcuna manutenzione.
Struttura a strati con uno spessore complessivo di 137 cm: La SUPER 2100-3i ha realizzato il binario senza ballast ,composto da uno strato di base unito idraulicamente e uno strato in calcestruzzo rullato e compattato, in sei passaggi.
Nella fattispecie del Tunnel Albvorland, i requisiti riguardanti la costruzione erano ancora più elevati del solito: l’impresa di costruzioni incaricata dell’esecuzione dei lavori dall’impresa generale Implenia Construction GmbH di Monaco di Baviera, la Kurt Gansloser GmbH, doveva posare ben cinque strati di base uniti idraulicamente con uno spessore di 25 cm ciascuno e uno strato in calcestruzzo rullato compattato di 12 cm di spessore nelle due canne a binario semplice e in un altro tronco lungo circa 3 chilometri. La larghezza di stesa era di 6,50 metri. In questo modo si intendeva portare la platea della galleria al livello desiderato e creare una fondazione per traverse e rotaie particolarmente resistente all’abbassamento. Allo stesso tempo, la Deutsche Bahn si assicura che il transito dei convogli non danneggi le linee sottostanti.
La struttura a sei strati presenta uno spessore complessivo di 137 centimetri
“Per lavori di questo tipo, tutto deve essere perfettamente coordinato. Precisione di pianificazione, una squadra esperta e macchinari performanti sono indispensabili”, dice Christopher Gansloser, amministratore delegato della Kurt Gansloser GmbH. “Soprattutto nei cantieri in galleria, l’aspetto emissioni gioca ovviamente un ruolo importante”. Per questo, lo specialista di costruzioni stradali e edilizia sotterranea ha optato per la finitrice grande SUPER 2100-3i di Vögele. La macchina della Highway Class presenta una capacità di stesa fino a 1.100 t/h e, con il suo moderno sistema di propulsione, è predestinata all’uso in galleria. Il motore è dotato di un sistema di post-trattamento dei gas di scarico multistadio comprensivo di filtro antiparticolato diesel e, quindi, soddisfa le severe linee guida della classe di emissione V europea. L’intelligente gestione del motore e il cosiddetto pacchetto EcoPlus, inoltre, riducono del 25 % il consumo di carburante.
La SUPER 2100-3i, inoltre, ha conquistato anche per la sua semplicità e intuitività di comando. Nonostante gli spazi angusti e la scarsa illuminazione, conducenti e operatori avevano una perfetta visuale di tutte le macchine e di tutte le zone del cantiere. I pannelli di comando ErgoPlus 3, infatti, sono retroilluminati e antiriflesso. Inoltre, vari proiettori a LED montati sul tetto della macchina, palloni luminosi aggiuntivi e faretti a LED nei pannelli di comando dei banchi illuminavano ampiamente l’intera zona di lavoro.
“Per lavori di questo tipo, tutto deve essere perfettamente coordinato. Precisione di pianificazione, una squadra esperta e macchinari performanti sono indispensabili“.
Christopher Gansloser, amministratore delegato della Kurt Gansloser GmbH
Per garantire una stesa di alta qualità, la Kurt Gansloser GmbH ha puntato sul banco estensibile AB 600: questo banco è estensibile idraulicamente fino a 6,00 metri ed è stato ampliato ulteriormente con elementi di allargamento per raggiungere la larghezza di 6,5 metri richiesta per la canna. Per ottenere la massima precompattazione possibile per tutti e cinque gli strati, la squadra ha utilizzato il banco AB 600 nella variante TP2 con tamper e due barre di compattazione. Le barre di compattazione idrauliche ad impulsi di Vögele sono uniche sul mercato e permettono di raggiungere valori di precompattazione fino al 98 %. In questo modo, la squadra di stesa è riuscita a garantire una qualità e un’efficienza di stesa elevate per tutti gli strati e a risparmiare tempo nei successivi passaggi di rullatura con i rulli tandem HD 10 VT e HD 13i VV di Hamm.
Lo standard di qualità per il piano di piattaforma, inoltre, richiedeva un controllo al millimetro dell’altezza e dell’inclinazione trasversale del banco di stesa. Il range di tolleranza per la posizione assoluta dello strato di calcestruzzo rullato e compattato di 12 cm di spessore era di soli ± 10 mm. Per osservare con esattezza questa tolleranza, per la posa in opera degli strati di base uniti idraulicamente l’impresa di costruzioni ha utilizzato il sistema di guida 3D wireless Navitronic Basic. Il sistema di Vögele è dotato di un’interfaccia aperta che permette di collegare i sistemi di posizionamento di svariati produttori.
La Kurt Gansloser GmbH ha utilizzato il sistema di Trimble. Mediante un’unità di controllo con tacheometro sono stati misurati le posizioni e i profili del banco e sono state calcolate le tolleranze. L’interfaccia ha trasmesso i risultati al dispositivo di livellazione automatica Niveltronic Plus di Vögele che li ha poi modulati. Per compensare le ultime ondulazioni del terreno, per lo strato di calcestruzzo rullato e compattato la squadra ha utilizzato il sistema a sensori Big MultiPlex Ski di Vögele. “In questo modo siamo riusciti ad attenerci alle tolleranze senza problemi e siamo estremamente soddisfatti del risultato”, ha detto Gansloser.
“L’alimentatore ha permesso di aumentare enormemente l’efficienza e la qualità e di risparmiare tantissimo tempo”.
Christopher Gansloser, amministratore delegato della Kurt Gansloser GmbH
La vera sfida consisteva nel fornire il conglomerato sul cantiere: ogni giorno, circa dodici autocarri con circa venti tonnellate di materiale ciascuno dovevano percorrere la canna in retromarcia per fornire il conglomerato. Parallelamente a ciò si svolgevano complessi lavori strutturali alla galleria, ostacolando ulteriormente la logistica. “Si trattava in parte di situazioni difficilmente pianificabili, pertanto all’inizio abbiamo dovuto adattarci”, ha spiegato Gansloser. “Dopo poco tempo, però, siamo riusciti a lavorare quasi senza interruzioni”. Questo fu reso possibile, da un lato, dai percorsi brevi verso l’impianto di confezionamento in loco e, dall’altro, dall’alimentatore MT 3000-2i Offset di Vögele: il PowerFeeder con una portata massima di 1.200 t/h ha permesso di trasferire il materiale alla finitrice in modo omogeneo e continuato. “L’alimentatore ha permesso di aumentare enormemente l’efficienza e la qualità e di risparmiare tantissimo tempo”, dice Gansloser. “Il cantiere si è trasformato in una perfetta combinazione di committente, progettisti, squadra di stesa e macchine”.
Caratteristiche salienti della finitrice Highway Class SUPER 2100-3i di Vögele