A road construction company from Altomünster shows how a thought experiment can give rise to lighthouse projects that influence an entire industry.Christian Schweiger had the idea of running his asphalt mixing plant in Aichach using renewables and so ensuring largely carbon-free production going forward. To implement this bold plan, Schweiger contacted Benninghoven – the first port of call for sustainable asphalt production. Fast forward four years... and in September 2023, the first virtually carbon-free asphalt mixing plant is now in operation, fired by wood dust instead of heating oil.
Wood dust burner instead of heating oil-fired
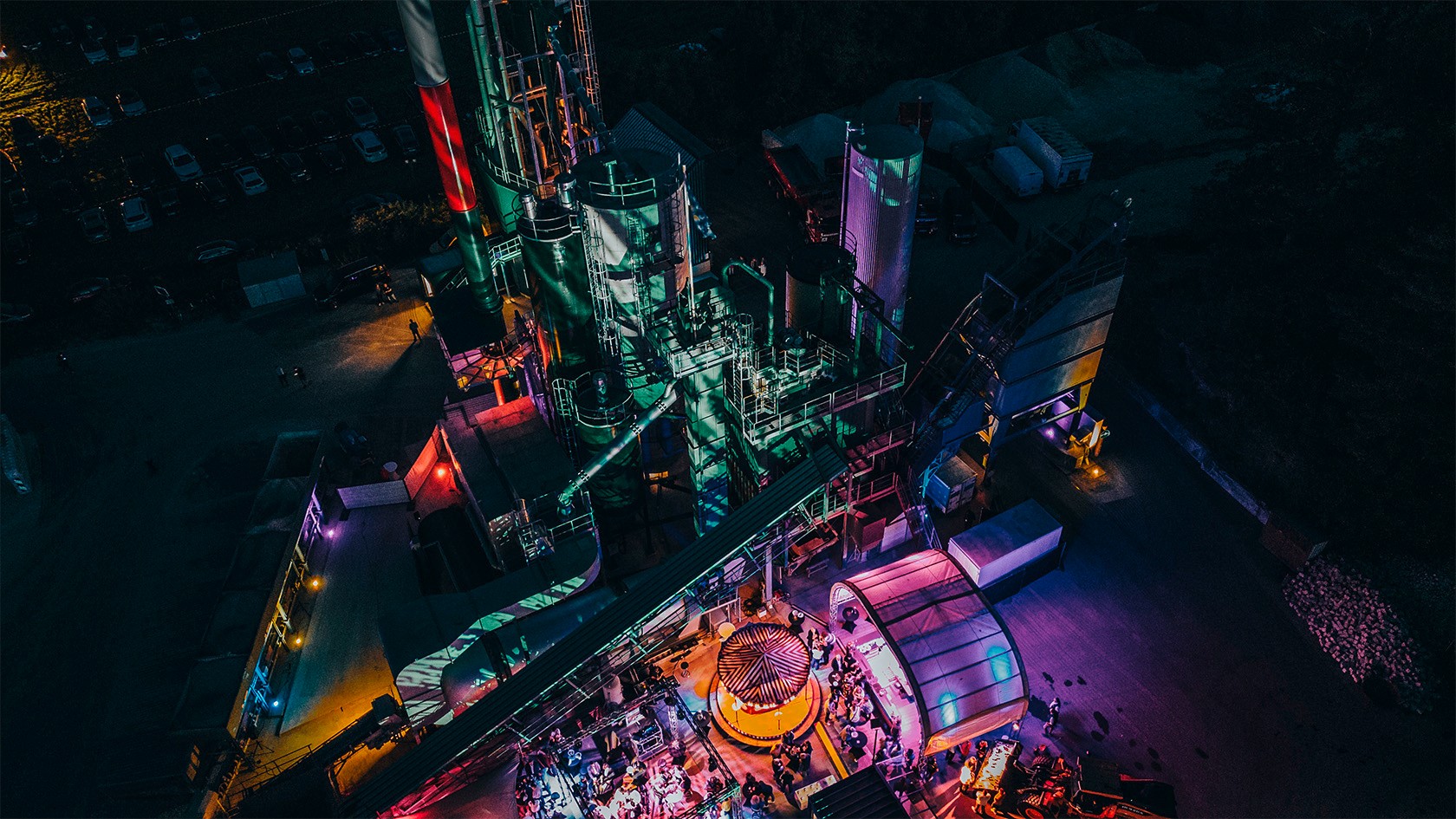