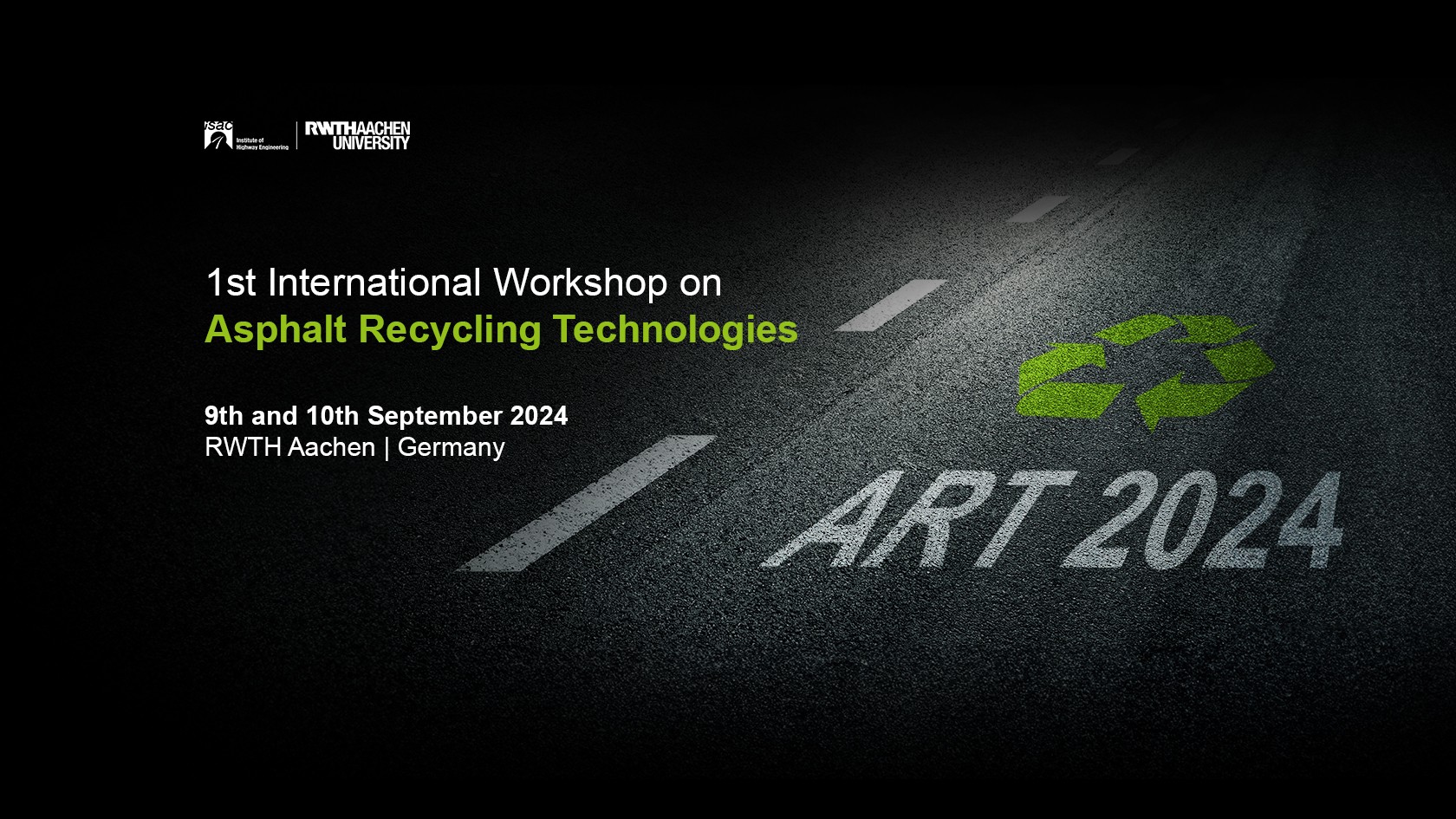
Select the right new machine or plant for your job site from our wide range of products. With our different brands, we – the WIRTGEN GROUP – cover the entire road construction process chain: processing, mixing, paving, compacting, and rehabilitating.