Im Stammwerk in Tirschenreuth können bis zu 20.000 Walzen pro Jahr produziert werden. Weil Tandemwalzen mit zwei Bandagen ausgerüstet sind, benötigt Hamm deutlich mehr als 20.000 Bandagen pro Jahr. Sie entstehen im über 11.000 m² großen Bandagenwerk just-in-time. Dadurch und durch kurze Dispositionszeiten kann Hamm sehr flexibel und schnell auf Marktanforderungen reagieren.
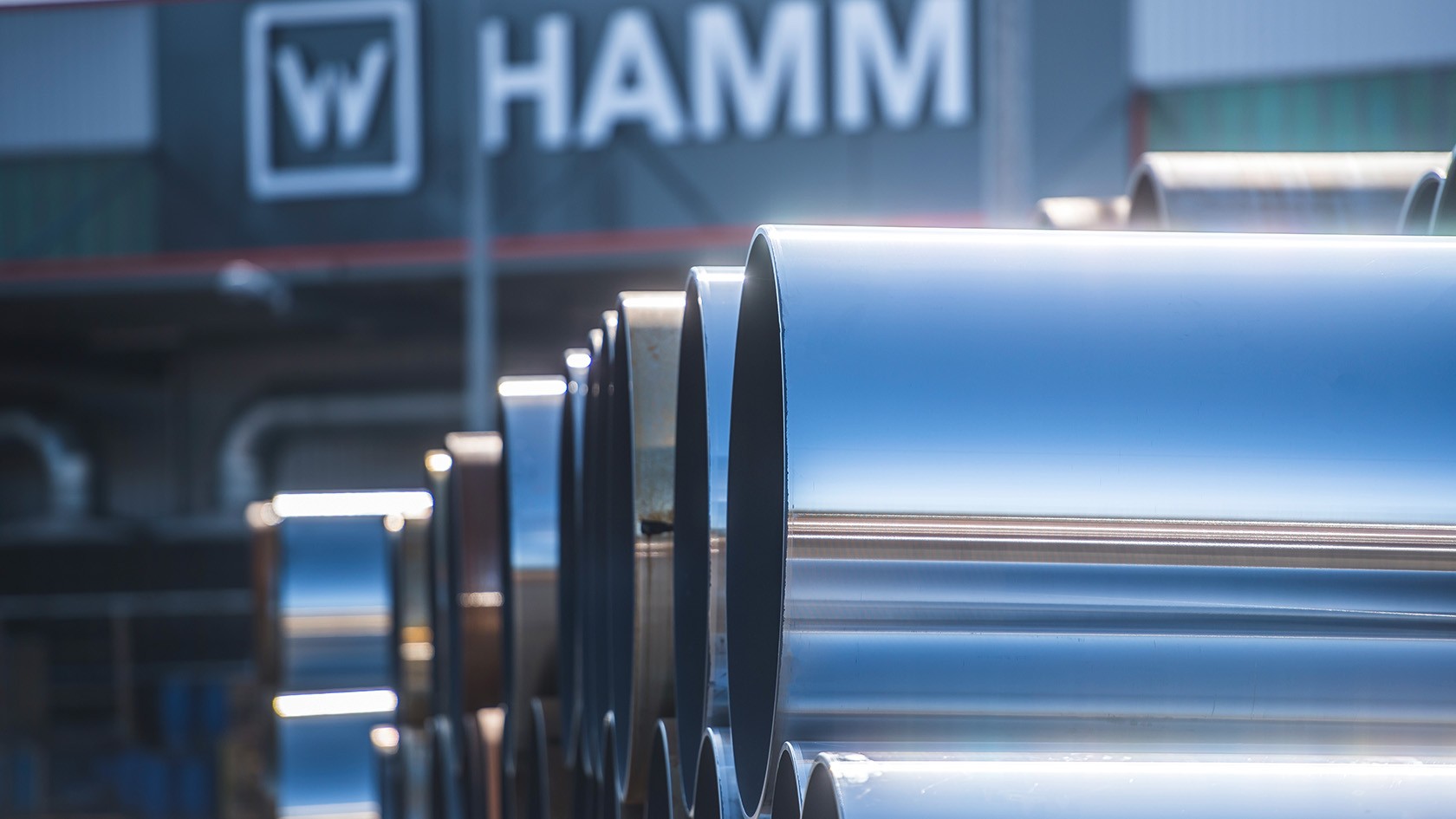