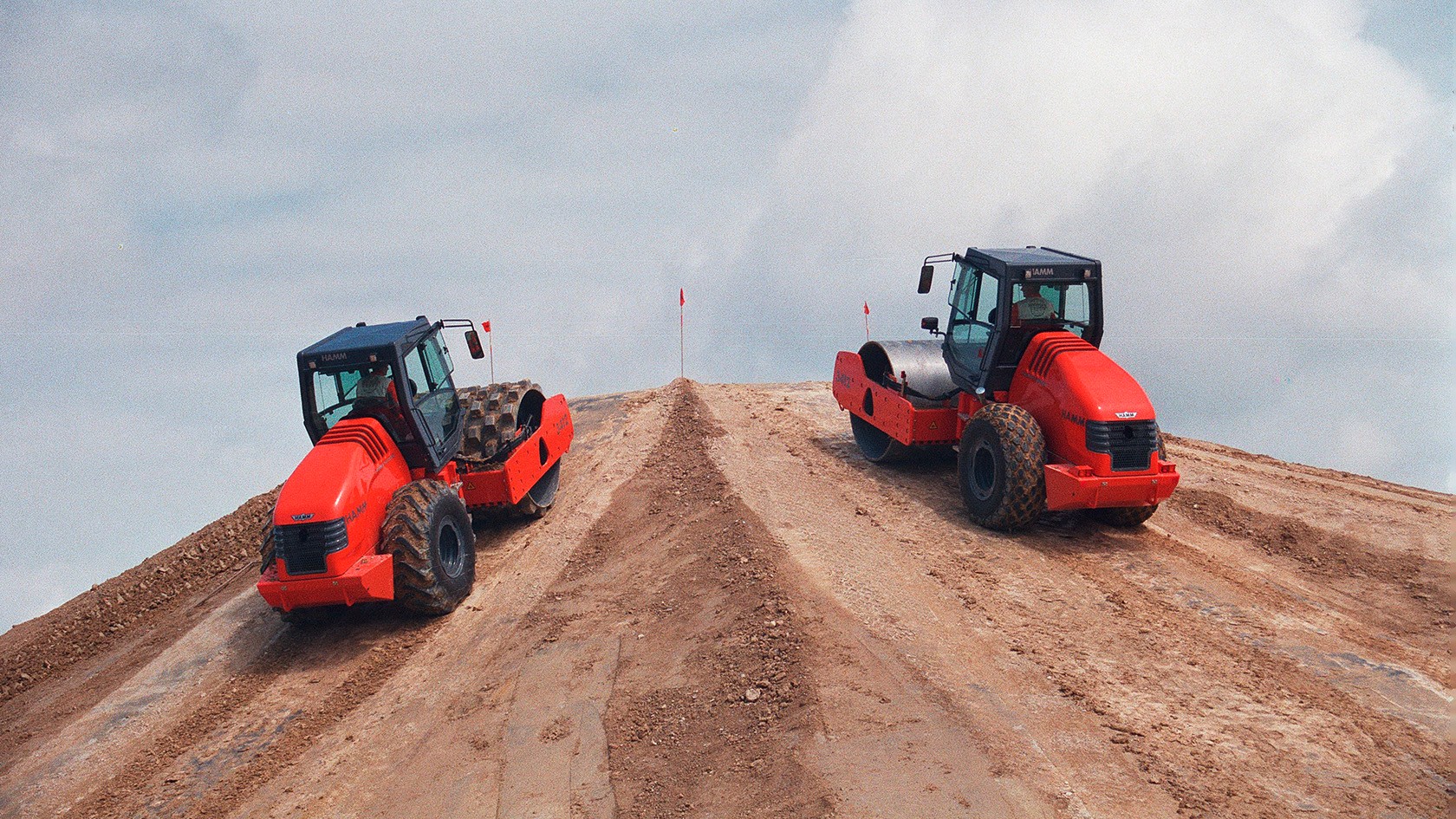
Powerful and "digital-ready"
The newly developed HC series from Hamm replaces the compactors from the 3000 and H series. Hamm has developed a uniform platform, offering models globally.
With options such as padfoot shells, dozer blade and vibration plate, Hamm is launching an unusually wide range of applications. Hamm has C models in all weight classes in its range for applications on difficult, steep terrain. Their gradeability is significantly increased thanks to an improved drum gear, improved hydrostatic drive, automatic Traction Control and a no-spin axle.
Large slope angles and powerful drives ensure that the compactors in the HC series achieve excellent compaction even on uneven and steep terrain – even on inclines over 60%.Thanks to the anti-slip control of the HAMMTRONIC, even a 25-tonne roller can be driven on a slope and on difficult terrain.
With operating weights of 11–25 t and a wide range of equipment variations, they are able to meet a wide range of requirements.
Thanks to new approaches in machine management, the HC series achieves increased overall performance, whilst also making savings. The HAMMTRONIC and integrated ECO mode ensure that the rollers work as often as possible in the economical partial-load range. The speed is reduced for this – but, thanks to a large travel pump and electronic hill-start assist, this is achieved without compromising the power. Overall, this concept saves fuel and reduces the noise and exhaust gas emissions. With the optional automatic engine stop, the energy consumption can be reduced even further. The use of non-fossil diesel completes the new sustainability package.
"In developing the HC series compactors, we have been able to bring together proven elements from two successful series in one common platform. This allows us to optimise the variety of parts and assembly processes and provide our customers with even better machines in terms of performance, ergonomics and sustainability."
Stefan Reber, Project Manager
The HC series has already been awarded the iF Design Award back in 2021. The international independent jury of experts awarded the prize for good product design, a strong operating concept, a high level of driving comfort and innovative and sustainable technical solutions. The two latest compactor series from Hamm – the HC CompactLine series and the HC series – were recently awarded the Good Design Award 2022 by the Chicago Athenaeum. These bring the total of internationally recognised design and innovation awards for successful products and developments received by Hamm since 1996 to 40.
Hamm has received a total of 40 internationally recognised design and innovation awards since 1996.
A new design for the front vehicle and scraper provides significantly increased clearance at the drum. This prevents material accumulations, meaning that cleaning work is correspondingly seldom required. For the steering, a new cast articulated joint with articulated joint lock allows for a greater steering and swing angle with improved kinematics. In addition, thanks to the optimised weight distribution in combination with the Traction Control, the gradeability is increased. Hamm is also improving compaction force: The centrifugal force has increased by up to 15% in comparison with previous models, and the static linear load is as high as 80.6 kg/cm.
Hamm has introduced numerous features to further increase the high level of operator comfort in the cab. More storage compartments, bigger treads and greater cab volume, as well as less vibration load and a reduced noise level, enable the operator to work comfortably. A new heating and air-conditioning system, the Easy Drive operating concept, the comfortable steering as well as the modern ventilation concept all round off the comfort provided by well-conceived construction machinery. In addition, Hamm offers various options to improve comfort on compactors with an open platform.
In terms of safety, Hamm offers a re-designed engine hood with view channel, which provides a clear view to the rear. The exterior rear-view mirrors are installed to be low-vibration and can be adjusted from the operator's platform. They can also be supplemented by an additional mirror with proximity detection.
Optional installation of 10-way lighting with economical LED lights ensures good visibility by day and by night. With the Coming Home function, the light remains switched on for a brief period before the spotlights switch off automatically.
Ready for a digital construction site
The 3000 series was one of the biggest development projects at Hamm AG in the late 1990s. A total of over 17,000 machines have been produced since 2000. Several series for local production in Brazil, India and China were also derived from this series. A wide range of products, represented on a platform concept, with a large number of innovations, such as the first generation of electronic machine control systems, the operator environment and the functional product design.
"I myself have worked for the Wirtgen Group since 1999 and have been working for Hamm AG since the beginning of 2000. The development of the 3000 series and launching the products on the market are clear highlights of the past 20 years."
Dr. Ing. Axel Römer, Head of Development and Construction
Every second roller sold in the world is an earthwork roller. Customers have strongly associated Hamm with asphalt compaction. Beginning with the 3000 series, Hamm has continuously expanded its market position in earthworks. The key factors for this success story have continued to be expanded and further developed, from the past generations of compactors through to the HC. Worthy of particular mention are the focus on design, ergonomics, quality, compaction power and digital technologies.
"[…] I have fond memories of 2001. At Bauma, we assembled a machine within a single day. It felt like an episode of "You Bet!". At the end of the day, a complete and fully functioning machine stood before us – we'd actually done it. […]"
Reinhard Schmeller (with Hamm AG since 1989)
"The distinctive silhouette, developed with the 3000 series, continues to characterise the appearance of the entire Hamm AG product portfolio to this day."
Ulrich Ewingmann, Dialogform GmbH
A well-designed machine offers a high level of user friendliness, sufficient space, well-placed operating elements and high usability. The 3000 series was the first generation of rollers whose design line was developed with the aid of a CAD design programme. In terms of design, the focus was now on rounded shapes, which gave the machines their characteristic appearance. Similarly, under the leadership of Werner Weihs, the 3000 series introduced the first machine design with free-form surfaces. In 2002, the 3000 series was awarded the iF Product Design Award.
"Before a machine is built as a prototype for the first time, it has already undergone a number of optimisations and improvements as a digital model. The findings of our customers, service employees and our production were taken into account in the new developments."
Dr Stefan Klumpp, Board of Management, Hamm AG
The demands on the products from the point of view of the customer as well as legal and normative requirements require constant further development of the products. The H series was first presented at Conexpo 2011 as the first Hamm-roller in the Tier 4 exhaust emissions category. As a result, the H series with engines compliant with the EU Stage IIIb/EPA Tier 4i exhaust emissions standard replaced the 3000 series in the European and North American markets, while the 3000 series continued to serve the EPA Tier 2 and EPA Tier 3 emissions markets. For all machines of the new H series, the HAMMTRONIC was included the standard scope of the machine. They were also the first Hamm machines with a die-cut engine hood. By January 2023, the exhaust emissions categories were adjusted twice more to the applicable legal standards.
"Both the 3000 series and the H series had their own special features. It was always fun to implement the respective innovations. The construction of the first machines with VC crusher drums was a particular challenge. These were partly assembled in standalone production, as line production was not initially designed for this purpose. It's good that everyone always pitched in."
Martin Würl (with Hamm AG since 2001)
The H series:
It is not only the striking design of the previous series that has been further developed. Innovations such as the Easy Drive operating concept and the HAMMTRONIC machine management system included as standard ensure even more efficient and sustainable working.
The H series compactors have experienced a consistent further development of the design. With the new generation of environmentally friendly diesel engines, the new Easy Drive operating concept was introduced into the compactors – a real milestone! Higher compaction power, additional, constantly improving options, such as the clear view dozer blade, the rock crusher and much more, are clear evidence of the continuous development of the machines. A total of 8,507 machines were produced in nine series in Tirschenreuth.