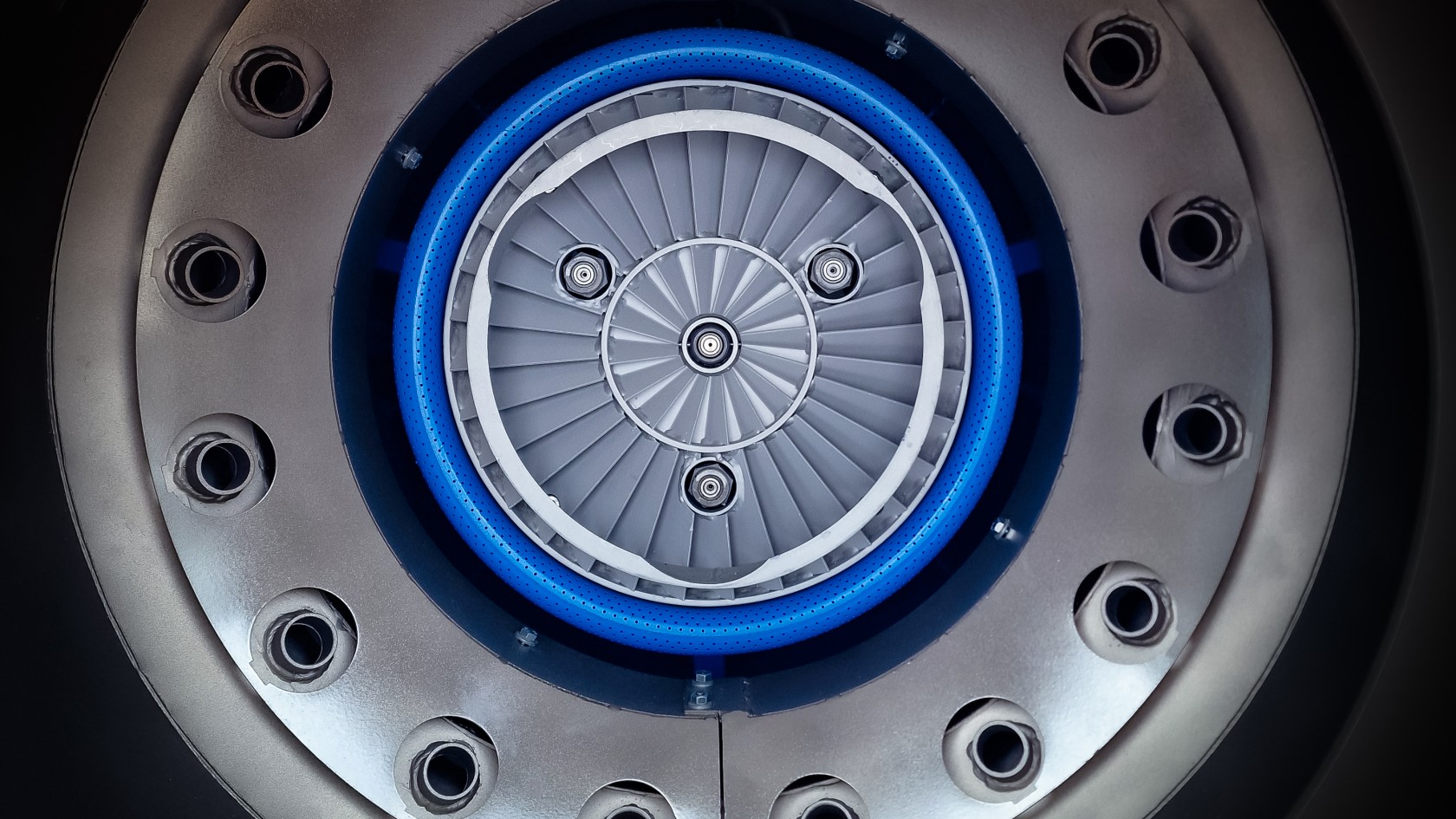
Benninghoven burners enable reliable use of renewable and therefore sustainable energy sources.
Many markets are now preparing to exit from coal, while systems running on oil are also increasingly subject to tighter regulations and restrictions. With technologies from Benninghoven, plant owners can modernize their plants and safeguard the continued operation of their site. EVO JET multi-fuel burners, which can use renewable fuels such as biomass to liquid (BtL) and wood dust, contribute to this. Both have a net-zero carbon footprint.
100 % green hydrogen system for road construction
With the world’s first burner that can be run with 100 % green hydrogen, BENNINGHOVEN offers a pioneering solution for more sustainability in road construction.
Everything from a single source – From the hydrogen source, the Benninghoven scope of delivery comprises the feed systems including the pressure control section, multi-fuel burner, hydrogen control section, burner control and plant components adapted to hydrogen operation.
In addition to this, the burner is supplied with a new control system. This coordinated hardware and software solution ensures an efficient process during asphalt production.
New plants as well as existing asphalt mixing plants can be equipped with the burner technologies from Benninghoven. Retrofit solutions can also be used for plants from other manufacturers. This gives any plant owner the opportunity to change to the latest technologies at any time – a key aspect for achieving economical and sustainable asphalt production and securing the future of the site in the long-term.
Download
Across the globe, climate action and tougher regulations from state and local governments are also challenging the asphalt industry to reduce their output of greenhouse gases such as CO₂. Owners of asphalt mixing plants have to reduce emissions to help secure the future of the plant site. When it comes to mixing asphalt in a cleaner and more sustainable way, changing from oil or coal dust to gas is a major step: Natural gas or liquid gas already halve the CO₂ emissions.
The outcome for the renewable fuels wood dust and biomass to liquid is even more impressive – these fuels are carbon-neutral. The fuels of the future are also attractive when it comes to their availability, as fossil fuels are not only limited, but are becoming increasingly more difficult to produce. This makes it even more important for plant owners to have the right technologies for using alternative fuels and to therefore be ready for the future.
“We are always thinking ahead and developing solutions for tomorrow. Apart from allowing the use of future fuels such as wood dust and BtL, we also focus on direct energy savings.”
Steven Mac Nelly, Head of Design & Development at Benninghoven
Energy from biomass
The principle of producing BtL fuels is based on liquefying biomass.
In the case of wood as a starting material, thermo-chemical conversion processes in a reactor use high temperature and high pressure to turn the cellulose-rich wood into pyrolysis oil.
The further processing steps include cleaning, synthesis and refining of the pyrolysis oils to produce BtL fuels.
Another significant development in the energy market is the use of biomass-to-liquid (BtL). BtL can be produced from plant waste such as straw, wood or energy crops like maize and oilseed rape. Benninghoven also offers an innovative solution for the use of biomass as a fuel:
the EVO JET BtL burner. Like wood dust, biomass-to-liquid is also considered carbon-neutral. And like all Benninghoven models, EVO JET BtL burners can also be run with other fuels such as oil, coal dust and gas. The new Benninghoven burners therefore offer plant operators a future-proof investment option: continuing to use fossil fuels in the short term while being ready to switch to renewable fuels quickly.
For wood or wood waste as a starting product, the challenge lies in processing a natural material that can vary in its chemical composition. These fluctuations affect the final BtL product. Smaller fluctuations can be compensated by adapting the preheating temperature. In the case of greater fluctuations or fuel changes, the settings have to be changed on site.
For new fuels, customers send their heating medium to Wittlich in a stainless steel container so the correct basic burner parameters can be determined at the BENNINGHOVEN factory. There, the fuel is tested extensively and the optimum burner settings are identified.
Still burning in the future
Wood is a renewable resource which can be produced sustainably and is therefore carbon-neutral when used as a fuel. With the EVO JET wood dust burner, Benninghoven has made it possible to burn wood dust in asphalt mixing plants – adding another product to the portfolio of burner technologies developed in-house. For plant owners, wood dust burners are a sustainable option of setting their plant up for the future.
The development engineers at Benninghoven have identified the ideal particle size of the wood dust, which is produced mainly from scrap wood and wood waste. Identifying the optimum grading curve for the fuel is important for the flame geometry of the burner – and therefore for the effectiveness of heating the virgin mineral or the recycled asphalt (RAP). Several Benninghoven customers are already successfully using the EVO JET wood dust burner.
The features of the solid burner offer the advantage that coal dust as well as wood dust can be used as a fuel.
A new burner can be adapted to coal dust as well as to the pioneering wood dust option.
But because supply issues are already emerging for coal dust now as well, wood as a carbon-neutral fuel is rapidly becoming more attractive.
The complete periphery includes the burner and the dosing unit. The inlet to the dosing unit is the interface to the customer systems. The wood mill and the wood silo are provided by the customer.
Burner
The wood dust is fed into the burner with precision dosing by means of the feed fan and the dosing unit. In the burner head, a separate auxiliary flame then ignites the material. The control range for wood dust with pilot flame is 1:6; the calorific value of wood dust is approx. 18 MJ/kg depending on the type of wood.
The secondary fuel is used for the pilot flame, e.g. heating oil EL, liquid gas or natural gas.
The wood dust dosing system with storage tank has a capacity of 2.5 m³ and is installed at the discharge of the wood dust silo. In the tank, two agitators prevent the formation of bridges in the wood dust. A speed-controlled dosing screw releases the fuel in accordance with the required burner output and transports the wood dust into a blow-through rotary valve, which forms the interface to the conveying pipe. From there, the wood dust is blown into the head of the burner with a feeder fan and pipe.
Raw material in the asphalt mixing plant
> Wood pellets
> Wood chips
> Wood dust
The owner is obligated to ensure that the overall plant (for example the silo with the dosing system) is checked as part of a regular inspection as per the German industrial safety regulations (BetrSichV). Outside of Germany, the systems are subject to mandatory testing – the applicable national laws and directives must be observed.
> Explosion protection (ATEX) especially for wood dust and coal dust
Liquid gas burner and natural gas burner
The BENNINGHOVEN gas burners can burn liquid gas already during the liquid phase, without first having to transform it into a gaseous state. This means that no additional periphery such as an evaporator and therefore no additional energy input is required.
Liquid gas burners and natural gas burners have the same mechanical structure. They differ only in their periphery, i.e. how the fuel is introduced into the burners.
> The fuel is gasified in the burner head while being mixed with the oxygen and then ignited.
> The burner head is made of highly heat resistant material.
> Its special design also determines the shape of the flame.
Liquid gas, referred to as “associated gas”, is generated during the extraction of crude oil or natural gas. This associated gas used to be simply released into the atmosphere or burned in many cases. Today, more and more regions worldwide have banned burning, which has an additional positive impact on the increasing availability of liquid gas.
Oil burner for light heating oil (heating oil EL)
Heating oil made from crude oil is divided into two types: light heating oil (heating oil EL) and heavy heating oil (heating oil S). The quality requirements for heating oil are defined in DIN 51603. Light heating oil can be burned in furnaces, central heating systems and industrial firing plants without preheating. Heavy heating oil, on the other hand, has to be preheated for transport and burning. The systems run with these fossil fuels, however, are increasingly subject to regulations and restrictions.
> BENNINGHOVENEVO JET burner, installed on the dryer drum
> For optimum drying and heating of the virgin mineral or recycling material – fired with extra light heating oil (EL) as a fuel
> Compressed air is used to create an explosive fuel/air mixture within the nozzle.
> This allows optimum atomisation of the oil particles on the largest possible surface.
> Then the fuel/air mixture is injected/atomised into the burner head.
> Compressed air 7 bar, oil pressure 12 bar.
> The advantage of this is a short, easy-to-control flame and high output regulating range of 1:8.
> Calorific value of extra light heating oil 42,700 kJ/kg
> Alternative: oil return flow nozzle
Coal dust burner (brown coal or hard coal)
Continuously rising energy costs and careful use of limited resources require innovative technologies and continuous further development. The burner type EVO JET was developed by the BENNINGHOVEN research team in practical application.
At the same time, the popular and proven user friendliness played an essential role in the development of the burner. The burner has a modular structure and is easily accessible.
To move the burner for maintenance purposes, it is set onto a corresponding chassis. Frequency converter technology allows the burner fan as well as the oil pump to operate in all control ranges, in perfect coordination. This means that only the actually requested consumption is used for drying in all performance ranges. The complete new development of the silencer combines noise reduction with improved combustion efficiency. This is achieved with the new positioning of the air intakes. The higher efficiency is due to the fact that the heat radiated by the face side of the drum is captured and the pre-heated air is guided to the burner. This means less energy is required for pre-heating the air. This helps to lower fuel costs. The burners from the EVO-JET series were developed for all fuels and have proven successful in practical application. The energy saving range is completed by the fact that BENNINGHOVEN already uses electric motors complying with the IE 2 (or IE 3) standard, which will become mandatory in the future.
> Coal dust is a solid, dust-type fuel that is made from brown coal or hard coal. This dust is produced during extraction of the coal from the deposit or the dust is specially produced in milling plants.
> Coal dust is a fossil fuel and is regarded as a cost-effective energy source.
> BENNINGHOVEN EVO JET burner – installed on the dryer drum
> Coal dust is fed into the burner with precision dosing using the supply fan and coal dust dosing.
> In the burner head, a separate liquid gas pilot flame then ignites the material.
> This flame switches off at a burner output of 20 % of the nominal burner output.
> The solid material flame continues to burn independently from this point or is automatically reactivated again when the value falls below the set parameter.
> The fuel of the pilot flame can also be used as an independent fuel.
> Control range 1:5 for coal dust only and 1:8 for coal dust with pilot flame
> Calorific value of coal dust: 20,900 kJ/m³
> Burner control, output control, coupled control and switchover between fuels are implemented with a type-approved control.
The BENNINGHOVEN EVO JET burner, which is designed as an oil burner in standard models, can be expanded to utilise up to three other fuels. This turns the burner into a combination burner, which means that other types of fuel such as oil, natural gas, liquid gas, heavy oil, BtL fuels (liquefied biomass) and coal dust are all available as fuels. The coal dust is fed into the conveying pipe with the aid of the coal dust dosing system (flange-mounted onto the outlet valve of the coal dust silo) and blown into the head of the burner with a feeder fan.
The clever coal dust dosing system offers users fundamental advantages with regard to:
> Functionality
> Fuel consumption
> Safety
Working more efficiently with sustainable and economical technologies is the challenge of today and tomorrow. Benninghoven offers a variety of innovative solutions for increasing sustainability in asphalt production.
Learn moreAsphalt production, recycling systems, combustion technology, control systems and bitumen technology – with BENNINGHOVEN technologies, every customer can find the right solution for their location, according to the specific requirements and conditions.
To the technologies