BENNINGHOVEN TBA 4000
in Belgium
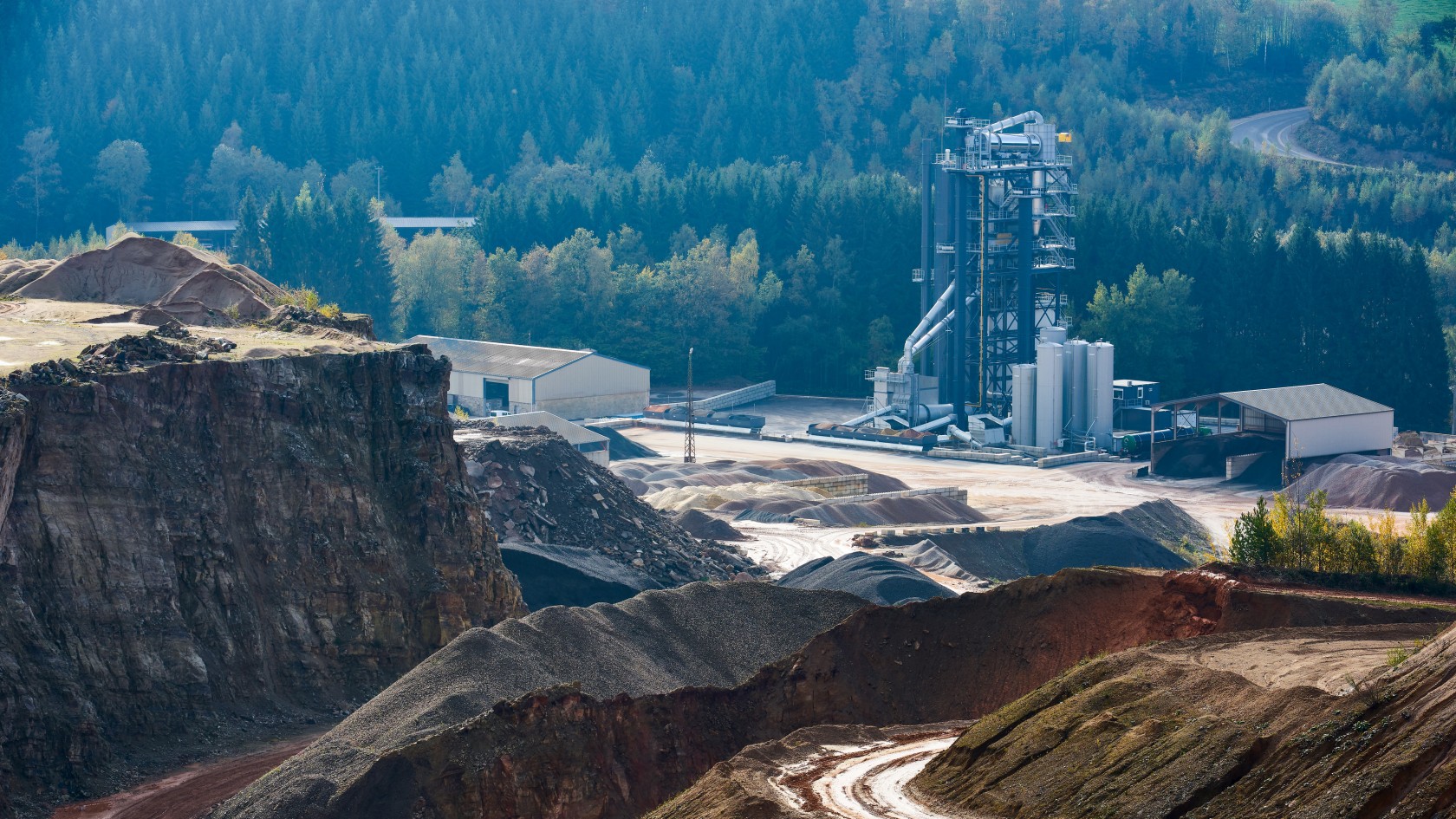
Inauguration ceremony for the first BENNINGHOVEN TBA asphalt mixing plant from the new factory in Wittlich
An opening ceremony in the pouring rain is of course not exactly ideal. But if the evening festivities end up being delayed, you do get a lot more time to spend with the main attraction. And so it transpired at a big company event organised by the Belgian construction company Bodarwé to mark the commissioning of a TBA 4000 from BENNINGHOVEN. A large number of guests attended despite the bad weather, and all of them were very keen to get a close look at the plant themselves and have the facility’s key benefits explained in great detail. All of which took place exactly 20 metres off the ground, in the weighing and mixing section that forms the heart of the plant. Overall, the mixing tower reaches 42 m into the sky. The plant, to be run by Bodarwé’s subsidiary Boreta S. A. in Baugnez near Malmedy, will use a wide range of recipes to make products from mixed goods, delivering these both to the company’s own paving team and other construction firms. The minerals required will be mined directly from the quarry next to the plant. “Our new TBA will be in full-time production from the start,” says Bodarwé’s Managing Director Michel Bodarwé. “We have a full order book and we’re looking forward to fulfil those orders with the new plant. Nor is it all merely about order volumes: the new plant will also improve our product quality.”
The new TBA 4000 is also a very special plant for its manufacturer BENNINGHOVEN: it is the first asphalt mixing plant to leave the new factory in Wittlich. At Wittlich, this WIRTGEN GROUP company builds asphalt mixing plants capable of meeting the requirements of customers and users all over the world. The company’s new headquarters, which are close to the German section of the Moselle and therefore purely by chance a near neighbour of the plant’s new home, represent the biggest single investment in the history of WIRTGEN GROUP. This new factory will further enhance BENNINGHOVEN’s international competitiveness. “Shipping out a new plant and seeing the satisfied faces of its new owners is always a great feeling,” reports Jean-Luc Didier, Head of Sales at BENNINGHOVEN. “And we can appreciate this only too well since the move to our new factory—because we’re also especially proud of our new location.”
Nor is this pride on the part of the asphalt-making specialists merely a result of the company’s impeccable infrastructure but also stems from its new product philosophy: based on the highest standards for quality and manufacturing as well as deeply integrated production, this has given rise to undreamt-of variety and a huge breadth of options. As a result, BENNINGHOVEN is now perfectly placed to meet future challenges—as is its Belgian customer.
BENNINGHOVEN TBA-type asphalt mixing plants
The Transportable BENNINGHOVEN Asphalt Mixing Plant — or TBA for short — is the universal, ‘all-rounder’ plant type within the company’s product portfolio. Suitable for both semi-mobile and stationary use, the technology used in TBA plants is characterised by its maximum flexibility and high-throughput plant performance that can run as high as 320 t/h.
The new product philosophy and the new factory were the key factors that guided Bodarwé’s procurement decision. “Buying the first plant from the new site was a conscious decision on our part. To put it simply: we were convinced by the benefits.” Which is not surprising: BENNINGHOVEN’s factory is equipped with a host of advanced technology while also setting the standards to follow for manufacturing systems. One of the many highlights here is the advanced surface treatment line that produces solvent-free powder coating. The scratch- and impact-resistant surfaces this process produces, together with permanent corrosion protection, are essential for a durable plant. All of which is very important for the client: “We’ve got big things planned for our TBA 4000,” comments Michel Bodarwé.
And the way is now clear: his construction company can use the new plant to produce and ship out large volumes at up to 320 t/h — thanks to a broad choice of optional systems, all of which naturally feature the trusted BENNINGHOVEN quality. Day-to-day reserves are provided by the mixed material loading silo, which has a capacity of 341 t. Some of the mixed goods produced will be sold on, while others will be used within the company, since Bodarwé also maintains a fleet of construction machinery from the WIRTGEN GROUP. The Bodarwé paving teams process the bituminous mixture with finishers from VÖGELE and rollers from HAMM.
With their recycling-friendly design and compliance with stringent global emissions regulations, BENNINGHOVEN systems are especially efficient and fit for the future. Thanks to two key technologies — a multivariable feed system and a parallel drum — the new Bodarwé plant can achieve recycling rates of up to 70 percent. BENNINGHOVEN classifies its recycling technologies into two types: cold feed and hot feed systems. Multivariable input is a cold feed system technology, which feeds up to 40 percent old asphalt directly into the mixer. The hot parallel drum feed system heats this stripped-out and reclaimed asphalt, and passes it as hot asphalt into the mixer. This procedure enables the greatest possible feed rate for the TBA. Technology for the highest recycling rate in the world — 90 + x percent — is also ‘Made by BENNINGHOVEN’. And for good reason: thanks to this recycling technology, reclaimed asphalt becomes a valuable resource that stays in the loop rather than problematic waste that needs expensive handling. And if the input rates required by law should increase, the TBA 4000 in Baugnez is still good to go. “Our new BENNINGHOVEN plant makes us fit for the future,” explains Mr Bodarwé.
This is all down to the new foam bitumen module, which is also integrated into the TBA 4000. And not by accident: use of this binder receives subsidies from the state in Belgium. This innovative technology can be used to produce low-temperature asphalts at a temperature of 110 °C, which is around 40 °C lower than the roughly 160 °C required for conventional asphalt. This, in turn, cuts the energy consumption for asphalt production by about 9 kWh/t — equivalent to 0.9 l heating oil per tonne of finished asphalt. CO2 and other emissions are also reduced. “While we’ve not yet brought the foam bitumen module online, the flexibility it offers is exactly the reason we opted to include it in our plant,” says Managing Director Michel Bodarwé. “This technology is certain to play a very important role for us in the future.”
Alongside technical features and benefits, operating companies are naturally also looking for first-class service provision. “With WIRTGEN GROUP and the BENNINGHOVEN Customer Support team, we have a partner we can absolutely depend on at all times — from major jobs like winter maintenance to the supply of spare parts or answering our day-to-day questions about plant operations.Whatever, whenever: they’re always there.” In Bodarwé’s case, the service technicians don’t have far to go, of course: the TBA 4000 is only a couple of hours’ drive away from BENNINGHOVEN.
Bodarwé Head of Service, Alain Heukemes: “The opening party for our first TBA went really well and we’re now looking forward with our customer to starting production. And we’ll obviously be staying involved with our first TBA 4000 in the future, too.” This is because BENNINGHOVEN’s new factory has boosted not just production but also its service: “The kind of customer satisfaction we have with Bodarwé doesn’t happen overnight: it’s always down to the effort of the entire Customer Support Team.”