Sustainability in a whole new dimension.
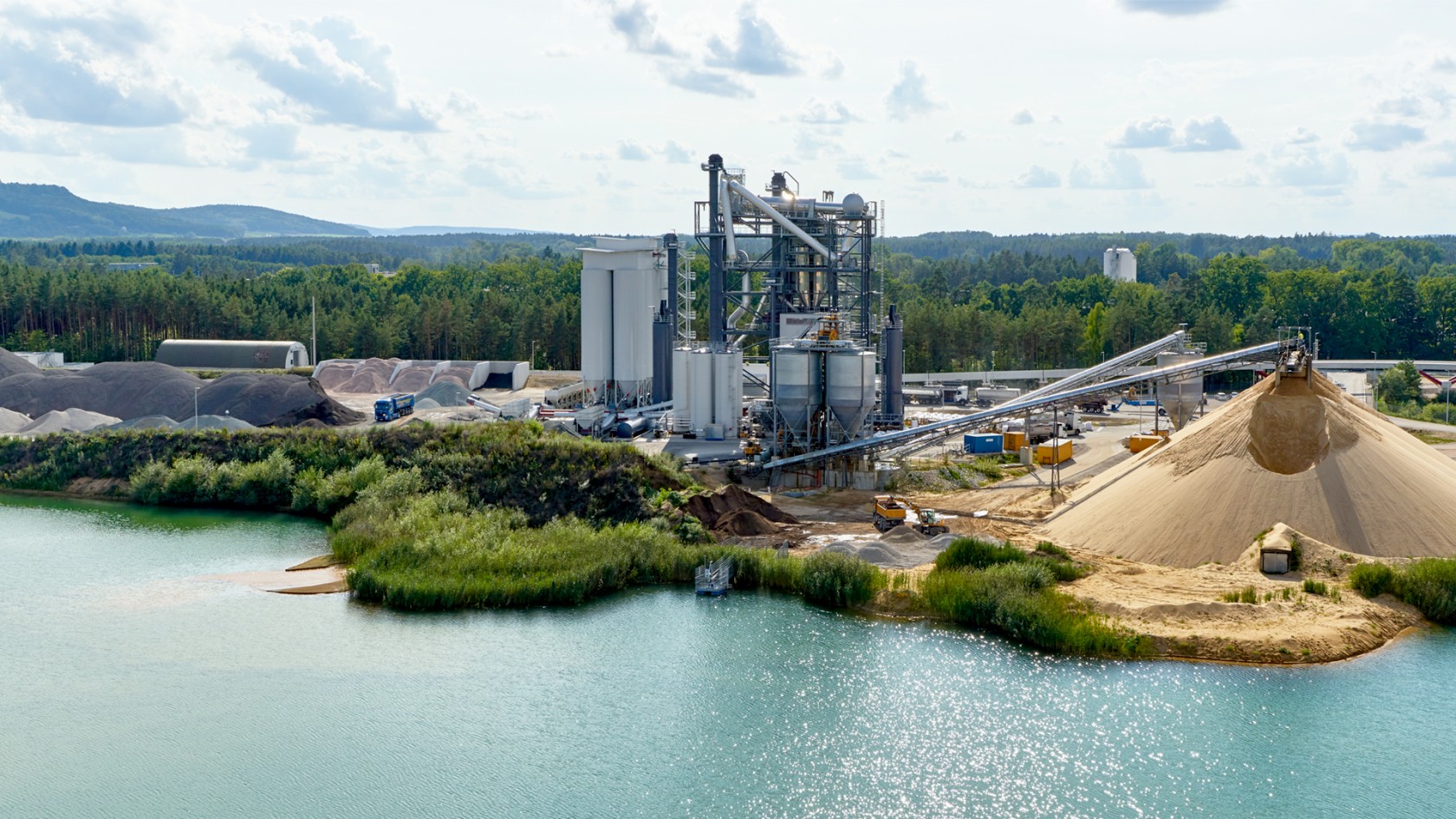
Investment in cutting-edge technology from BENNINGHOVEN: the new BA RPP 4000 asphalt mixing plant operated by the Max Bögl Group at its Sengenthal site is the backbone for many road construction sites in the Nuremberg region. The most important innovation is a hot gas generator with a counterflow parallel drum system that supports RAP material rates of 90 + X% – with minimal emissions. The plant had already met with an enthusiastic response from professionals of the industry at bauma 2016.
Ready for the asphalt production of the future: the new BA RPP 4000 operated by the Max Bögl Group is something special. Located in Sengenthal, the plant supplies some 2,000t of hot mix to job sites across the region every single day. Depending on the formula, about 1,800t of the mixes can consist of RAP. That is because the recycling innovation from BENNINGHOVEN, the counterflow parallel drum system with hot gas generator, can work with RAP material rates of 90 + X %. The unique technology also delivers a massive reduction in emissions, making investment in this green and efficient technology particularly sustainable and forward-looking. After all, in industrialized nations such as Germany it has long been the case that far more miles of road are rehabilitated than built from new – which also means that millions of tonnes of asphalt are removed. This task is largely handled by cold milling machines, which at their peak can load up to 3,000t of milled material onto lorries in a single shift. The residual waste from such operations has long posed a challenge for road construction contractors.
The recycling technologies of BENNINGHOVEN transform RAP – in the form of aggregate in a variety of grain sizes and the binder bitumen – into “black gold”. In many countries, almost every lorry delivering material to a job site carries a proportion of recycled asphalt. This is evident from the fact that out of a total of 40 million t each year, 12 million t of recycled asphalt are now being laid by road pavers – and that’s just in Germany. Across the world, too, RAP is increasingly being discovered as a resource. In response to this trend, BENNINGHOVEN have developed the counterflow parallel drum system with hot gas generator to market-maturity. “The main advantage of the technology is that it combines sustainability and efficiency to profitable effect,” says Markus Bühl, Consulting and Sales, of the WIRTGEN GROUP sales and service company in Augsburg. This was one of the clinchers for Max Bögl, prompting the company to invest in a completely new plant rather than modernize the existing one.
The BA RPP 4000 comes with a second recycling technology as well – the multivariable cold feed system, which allows up to 40% RAP to be fed cold into the production process. This means that even small mix quantities from 2t can be produced, giving mixing plant supervisors great flexibility. Thanks to the high-performance plant, Max Bögl will immediately be able to supply a wide range of different road construction sites in the Nuremberg area with mix from Sengenthal – using its own fleet of temperature-controlled lorries.
Hot feed system: counterflow parallel drum system with hot gas generator for RAP material rates of 90 + X%
The cutting-edge technology stands for the highest rate of RAP in asphalt recycling worldwide. The recycling material is heated to the optimum asphalt processing temperature of 160°C in a parallel drum – in counterflow, as with aggregate obtained from quarries. Unlike in conventional asphalt production, the burner heats the RAP indirectly, i.e. with hot gases, to ensure that the bitumen contained in the asphalt does not burn while keeping emission levels within the normal range.