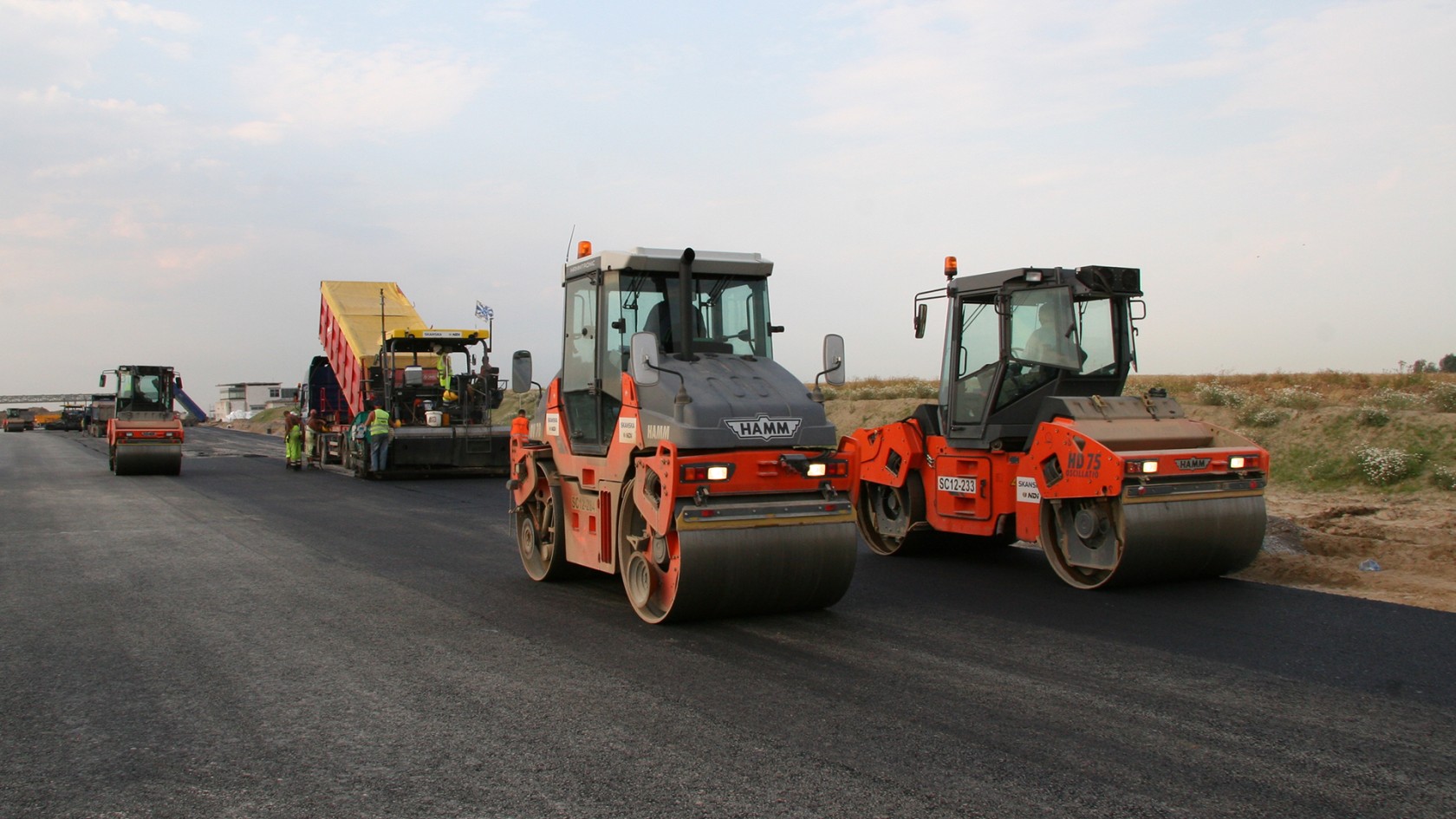
Even in ancient and medieval times, roads were the main arteries of international trade. One of the most important routes was the Silk Road, which ran from Turkey to East Asia. Its European counterpart, the Amber Road, led from the Baltic region across the Baltic coast, through what is now Slovenia and right up to Venice. Poland was, and still is, an important transit country between northern and southern Europe and between western and eastern Europe. The construction of a new motorway will open up both Poland and Europe to many advantages for trading and commerce.
Functional transport links are an essential component of a thriving economy. The prospective A1 is one of the ten most important transport axes crossing Europe, from the Atlantic to the Volga and from Scandinavia to the Mediterranean. Once fully developed, it will connect the Baltic seaport of Gdansk with Vienna and southern Europe, via the Czech city of Brno and the Slovakian capital Bratislava. 582 kilometres of this route will be on Polish soil. At the end of 2005, work began on the first section to be constructed. It runs from Rusocin, not far from the seaport of Gdansk, 90 kilometres inland to Nowe Marzy.
Thorough planning – the basis for success
The Swedish/Polish Skanska-NDI joint venture received the contract for planning and constructing what was then the biggest asphalt construction project in Europe. The new transport axis aimed, however, to do more than "simply" satisfy the requirements of modern highways. Skanska-NDI also places real value on efficiency. This meant that the consortium worked using efficient processes with high-quality machines and methods, which guaranteed the long-term quality of the carriageway and allowed the motorway to be completed on schedule.
The A1 – an environmentally friendly project
By building a motorway, humanity is always encroaching into natural habitats. That was also the case when building the A1, but this was adequately compensated for. For example, a number of wildlife bridges were built that will allow deer and boars to continue crossing to the other side of the motorway in future. Storks are another species whose habitat is affected by construction work. They are common across Poland, and, in some villages, even make up the majority of the population. Where individual yards were too close to the new roadway, storks' nests were taken very cautiously and with extreme care to other places where the storks can raise their future young. But commitment to cleaning up the environment does not stop here. Skanska-NDI places real value on environmentally friendly methods and machines that consume little fuel and minimise noise and exhaust gas emissions. Recyclable materials are used where possible.
An organised dynamic
The implementation of the project was characterised by clear specifications and single-mindedness. Travelling along the major construction site, 90 kilometres in length, made it clear that everyone here knew what they had to do. The work was done in an extremely coordinated and considered way. Countless teams were employed in parallel for building bridges, earthworks, hydraulic engineering and paving the carriageway. Skanska achieved this with well-trained personnel, regular communication and transparency. This is just as much a part of the project as proper documentation. And, despite this, there were and always will be unforeseen occurrences that require the teams to be flexible and creative. These occurrences range from capricious weather to archaeological finds and bombs from the Second World War. But so far, the Polish building experts have found a solution for every fresh challenge, meaning that the project is still perfectly on schedule even after two years – unlike many other major projects.
Making use of expertise to achieve your aim effectively
The employees for paving the carriageway have been recruited from many different construction companies. This is why the level of knowledge and wealth of experience varied greatly within the individual paving teams when the work began. Through comprehensive training, Skanska-NDI has managed to get all paving crews to the same high level of knowledge, as well as being perfectly versed in its machines and paving methods. Employee expertise was one of the success factors in the construction of the A1. Because paving and compaction is done almost exclusively by HAMM and VÖGELE machinery, WIRTGEN POLSKA organised training dealing with operating VÖGELE pavers and HAMM rollers, but also with application technology and questions about asphalt paving. It was clear right from the beginning here that the courses would be held in Polish. This is a must if you want to guarantee the maximum transfer of knowledge. The fruits of this thorough preparation became apparent very quickly, as Skanska-NDI made optimum use of the possibilities offered by the HAMM rollers, and consequently operated the compaction machines extremely effectively.
Safety – a must on the construction site
In addition to technical data and productivity, safety also plays a key role. Active and passive protective measures have so far ensured that Skanska is one of the companies with the lowest number of accidents worldwide. HAMM rollers suit this approach perfectly. The 3000 series compactors and the HD series tandem rollers will impress you with their large panoramic cabs, from which drivers have good all-round visibility at the construction site. Other important features include the ROPS cabins and the clear symbols on the operating elements. The safety engineers at Skanska-NDI particularly like the DV series tandem rollers – the rollers where the operator is always driving forwards. Increased safety is the idea behind this!
Machinery from the WIRTGEN Group – to ensure quality
"I have selected only the best machinery for this demanding project." This was said by someone who ought to know – Mariusz Gielniewski is responsible for procuring and operating the well over 600 construction machines used in this project. There was, therefore, no alternative to the asphalt construction machines of the WIRTGEN Group. After all, HAMM, WIRTGEN and VÖGELE machinery not only boasts the appropriate technologies for building a state-of-the-art motorway, but will also impress you when it comes to uptime, productivity and service quality. It was not in vain that a total of 99 machines from the WIRTGEN Group were used in July 2007 at this construction site – including close to 80 HAMM rollers. The full service offered by WIRTGEN POLSKA undoubtedly also contributes to the high uptime. A team of service technicians works permanently on site at the builder's yard in Rusocin. There, they take care of any necessary maintenance work, which, at the wish of Skanska-NDI, is carried out in strict accordance with the manufacturer's specifications. But they also do other servicing work, for example retrofitting chip spreaders on tandem rollers. Of course, the professional team has the most important spare parts and wear parts in storage at the construction site. Should a part nevertheless be missing, help is available from colleagues at WIRTGEN POLSKA in Poznań or plants in Germany quickly and without complications.
The birth of a motorway...
Motorway construction is always a highly complex project. The complexity increases with length here, because each new kilometre brings new technical requirements with it, due to the topography and changing ground characteristics. Planning, organisation and logistics are just as challenging when it comes to construction. Very soon after the project began, the first machinery from the WIRTGEN Group was in use, enabling the smooth running of seven nearly parallel stretches of the 90 kilometre section of the A1.
Phase 1: Earthworks
A solid substrate is a decisive factor in the operating life of a motorway. Unfortunately, the soil available did not always have the technical properties desired for this project. There was insufficient load-bearing capacity or the soil could be compacted only with difficulty. This is why, by summer 2007, around 20,000,000 m3 of earth had been replaced. The newly introduced soil was then consolidated with the remaining material in several areas. Strong teams were required for this. A total of ten WIRTGEN soil stabilisers of the WR 2500 S and WR 2000 types mixed the pre-spread binding agent into the soil, which was immediately compacted by HAMM compactors. This process improves the plasticity, immediately increasing the load-bearing capacity. In most cases, a 3412 HT compactor with a smooth drum works behind the soil stabiliser. Where the water content was still too high, the 3412 compactors with a padfoot drum were used.
Phase 2: Frost protection layers
Frost protection layers have a great influence on the durability of a surface course, because they prevent frost damage to the pavement by draining away the water. When constructing these layers, Skanska-NDI relied on VÖGELE's high-compaction technology and HAMM's compaction technology for many sections. The crushed rock was paved by pavers of the SUPER 1900-2 type. A team of three HAMM rollers took on the compaction of the mixture of basalt and granite, imported from Scotland. The HD 120 works with vibration, the HD O 90 V compacts with oscillation and the GRW 10 introduces its working weight in the event of high static linear load.
Phase 3: Asphalt construction
The first phase, asphalt paving, involved the most work for the HAMM rollers, as the 90 kilometre carriageway had to be built over with four layers of asphalt. This included two 7.5 centimetre layers as a base course, an 8 centimetre thick asphalt binder course and a 3.5 centimetre thick layer made from stone mastic asphalt. Skanska-NDI used the rollers in groups, with properly coordinated working weights to compact all layers. An HD 120 tandem roller (working weight 12 t) always worked together with two to four type HD O 90 V or HD O 75 V rollers. How many machines were used depended mainly on the width of the carriageway. All 7 and 9 tonne rollers were equipped with an edge cutting device and an edge pressing device. This is why one of them was used to work on the edges. Meanwhile, the others took care of the swift rise in the degree of compaction and the smoothing. Where there were a particularly large number of edges to work on and joints to compress, Skanska-NDI also made use of the advantages of the DV 70 VO all-wheel steered tandem rollers. They are characterised by great manoeuvrability and an outstanding view of the carriageway and drum edge. The construction manager for the whole A1 used them in all places where sensitive regulation and manoeuvring was especially important for a high-quality carriageway. Mariusz Gielniewski explains why, saying that "they are the most ingenious and technically sophisticated rollers that I have seen to date. We always use them when things get tricky."
Oscillation: Increased efficiency and economy
The 12 tonne rollers worked on this construction site with vibration or in static mode. For all other tandem rollers, compaction was with oscillation and vibration – and, in fact, according to well-developed rolling patterns. This is how they achieve the optimum degree of compaction, while using as few machines and taking as little time as possible. Efficiency is what counts! What is particularly interesting here is taking a look at bridge construction, as there are a total of 86 bridge constructions along the first 90 kilometres of the A1! Mostly, these are viaducts or wildlife bridges across the motorway, but there are also five longer viaducts underneath. Oscillation rollers have ensured especially efficient work there. With this form of dynamic compaction, the degree of compaction increases quickly without the risk of over-compaction. At the same time, however, only 15% of the vibrations that would come from vibration rollers would be produced. This is why oscillation rollers can also be used for dynamic compaction on structures sensitive to vibration. Skanska-NDI very quickly recognised the added value of HAMM's oscillation, and consequently also uses this technology for asphalt paving everywhere else. Mariusz Gielniewski knows that "with oscillation, we can achieve the desired degree of compaction faster and with fewer passes, and consequently require fewer operating hours." For four asphalt layers on a four-lane, 582 kilometre motorway, this is certainly a significant cost factor.
Compactors
Tandem rollers
Pneumatic-tyre rollers