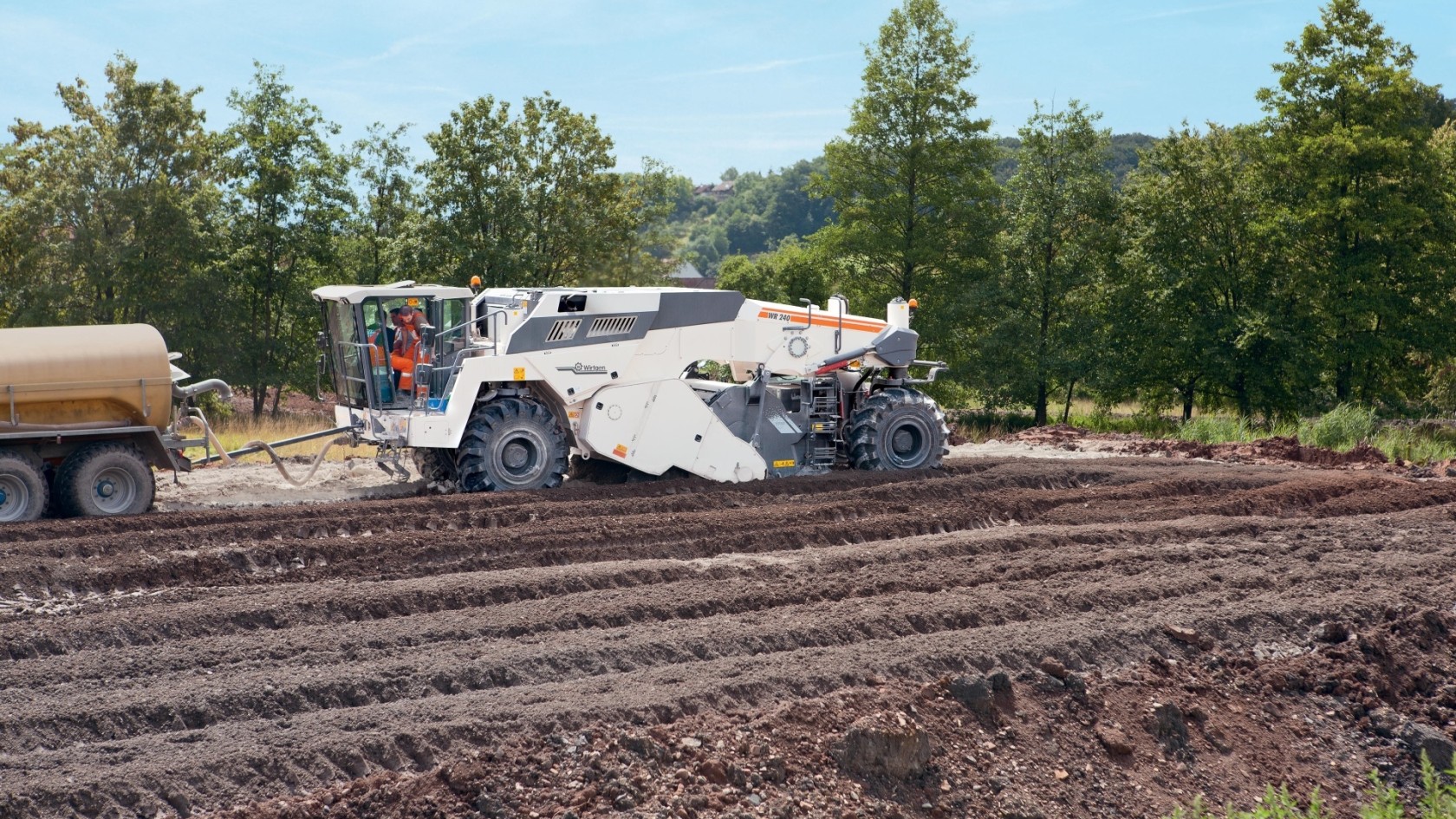
Five very different job sites, but the same picture throughout: the Wirtgen WR 240i elegantly works its way through or over the base, regardless of whether it is stabilizing heavy, boggy ground or recycling a stretch of motorway. The first member of a new generation of soil stabilizers and cold recyclers from Wirtgen, the machine underwent initial field tests in Germany, achieving top marks for its performance, user-friendliness and the quality of the final product.
A dam up to 6 m high will in future divert inflowing water into a landscaped detention basin near Tübingen if necessary in order to better protect the town from flooding. The contractor used a WR 240 / WR 240i soil stabilizer and cold recycler from Wirtgen for this technically very demanding construction job. To build the dam core, the soil was improved by backfilling 50-cm-thick layers of soil and pre-spreading binder (50% lime / 50% cement) which were then homogeneously mixed in by the WR 240 / WR 240i while adding water at the same time. The recycler finally stabilized the soil to produce the water-tight dam surface by mixing backfilled material with pre-spread binder (30% lime / 70% cement) and water just as homogeneously to a depth of 50 cm.
The water is supplied by tanker trucks and injected directly into the rotor housing in precisely metered quantities.
To ensure the dam's resistance to erosion and washout, high standards were specified with regard to the mix quality. Precise adherence to the specified water content was of particular importance.
State-of-the-art metering technology ensured that the WR 240 / WR 240i fully met all demands in respect of precise adherence to the specified water quantity. The actual water content is also conveniently displayed on a screen. Optimum traction and large ground clearance allowed the recycler to make swift headway on the soft, clayey soil as well as on steeper sections of the terrain when producing the dam surface. The outstanding manoeuvrability of the WR 240 / WR 240i and a reversing camera with reverse assist function not only made reversing easier, but also permitted time-saving manoeuvres to evade the dozers, excavators, tractors and spreaders operating on the site.
In view of the anticipated high traffic volumes with a correspondingly high percentage of heavy traffic, rehabilitation of the A7 motorway near Langenau called for both a sub-base and upper pavement structure of superior bearing capacity. The WR 240 / WR 240i was commissioned to produce a hydraulically bound base course of high quality. In a first step, water and base course binder (15 kg/m²) were distributed on the subgrade level previously produced by graders. Hydraulic binder was then accurately and homogeneously mixed into the existing gravel material at a working depth of 30 cm by the Wirtgen soil stabilizer and cold recycler. The WR 240 / WR 240i stabilized an area of 16,000 m² altogether and ensured that the hydraulically bound base course could be handed over to the subsequent project divisions on schedule. Characterized by perfect evenness, superior bearing capacity, water and frost resistance, the hydraulically bound base course now forms a stable foundation for the new section of the A7 motorway.
The WR 240 / WR 240i stabilized the sub-base by powerfully and homogeneously mixing the various materials.
The WR 240 / WR 240i performed impressively, paving the base true to line and level, as the automatic cross slope control prevented any displacement of material on the previously produced subgrade. Height adjustment ensured that the working depth was constantly maintained. The powerful milling and mixing rotor created a homogeneous mix of high quality ensuring that the hydraulically bound base course met with the highest standards. What's more, the mixing concept with perfectly matched rotor and rotor housing produced mixes of superior quality in a short period of time, enabling the WR 240 / WR 240i to stabilize the soil at a high rate of advance resulting in economic operation and high daily output rates: 10,000 m² of soil were stabilized every day on this job (during an 8-hour shift).
The surplus soil excavated during the production of line cuts and tunnels when building the new ICE railway line between Ebensfeld and Erfurt was transported to a nearby stockpile where it was stabilized by adding binder before being used to backfill bridge approaches, sewer trenches, etc. along the railway line.
Highest quality standards had been agreed: to achieve a particularly homogeneous mix (grading curve < 25 mm), the customer specified thorough mixing in three passes. Consequently, the WR 240 / WR 240i first homogeneously mixed pre-spread binder (up to 90 kg/m²) into a 50-cm-thick layer of soil. In the next step, the soil was thoroughly re-mixed while adding precisely metered amounts of water before being homogenized by the WR 240 / WR 240i to make it suitable for placing.
All the main basic functions are easily and conveniently controlled by the machine operator via the highly precise multi-functional joystick integrated into the right-hand armrest. Automated processes, such as automatic lowering and raising of the milling and mixing rotor, the ergonomically designed workplace and the innovative reverse assist function, make life vastly more convenient for the operator. The extra large steering angle of the rear axle permits swift turning manoeuvres at the end of the short passages, as well as in confined conditions. These advantages improve operator performance.
High engine power and optimum traction allow the WR 240 / WR 240i to work its way through the heavy soil without difficulty. The powerful, directly driven rotor with rotor speeds adjustable from the operator's cab and perfectly matched rotor bars ensure consistently perfect mixing quality. This was also confirmed by every check undertaken by the testing laboratory which closely monitored the quality of stockpile production.
Areas adjoining the nearby river Main had to be stabilized during construction of the ICE railway line between Ebensfeld and Erfurt. To this end, soft slate with a grain size of up to 350 mm from a tunnel excavation was transported to the relevant areas, piled up by dozers and then precompacted and de-tensioned by Hamm compactors. To produce a finer grain size, the exceedingly coarse material was homogeneously granulated by the WR 240 / WR 240i at a milling depth of 50 cm in a single pass. In this way, the surface was optimally prepared for thorough re-compaction.
The WR 240 / WR 240i is an ideal candidate for such tough jobs. Operating in difficult terrain, it granulated the material in a single pass thanks to its large milling depth. High engine power, a powerful direct belt drive, impressive cutting performance and high rates of advance are crucial here. A robust rotor housing with rotor optimized for performance is essential to produce the specified small-size material at a high rate of advance. Although granulating the large rocks produces considerable noise and vibrations, these disturbances are not felt in the soundproof, vibration-damped cabin. Even high summer temperatures, the operator stays pleasantly cool in his spacious, ergonomically designed cabin, for an efficient automatic climate control system ensures relaxed productive working in all weathers.
Material with a grain size of up to 350 mm had to be crushed to a depth of 50 cm in a single pass. On site, the WR 240 / WR 240i achieves high daily output rates of up to 12,000 m².
In Frensdorf, Bavaria, the WR 240 / WR 240i was commissioned to stabilize the soil of a school playground. After pre-spreading the 1,350 m² area with 37 kg/m² binder (making 50 tonnes altogether), the powerful stabilizer homogeneously incorporated the mixture of lime and cement into the soil at a working depth of 30 cm. The confined conditions, existing fixtures and walls directly adjoining the job site made good manoeuvrability and a clear view of the various obstacles an absolute must. The WR 240 / WR 240i mastered the job in next to no time.
Even on this small site with its extremely confined conditions, the WR 240 / WR 240i did an excellent job. The machine operator can choose from three different steering modes and mobility is further enhanced by additional steering of the rear wheels. All actions needed to execute the partly automated functions are intuitively realized via the multi-functional joystick integrated into the right-hand armrest. Thanks to the comfortable, individually adjustable seat and innovative visibility concept, the operator can complete the entire job in an ergonomically seated position. A comprehensive camera system is the main feature of the visibility concept: four cameras optimally positioned around the recycler and the reverse assist function ensure that all the main work situations are conveniently displayed on two screens in the cabin.
Agile manoeuvring is called for on the confined site. Large steering angles made for small turning radii and therefore swift progress.